Six things to consider when designing a transfer station
Best practices for incorporating durability, cost savings, and safety into municipal solid waste transfer stations
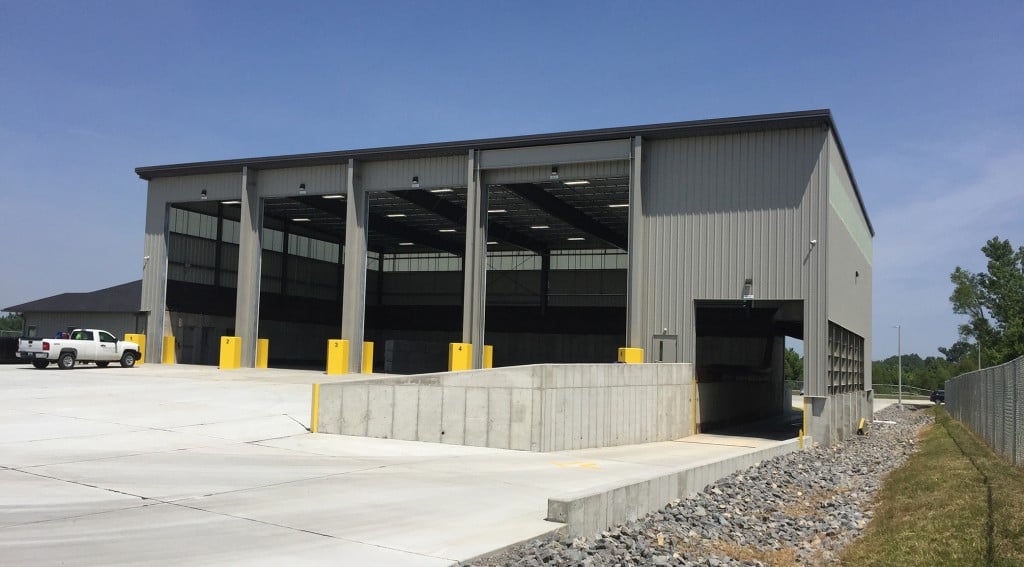
At its core, a municipal solid waste (MSW) transfer station is about convenience. It is meant to be a better location to dispose of end-of-life material than the landfill. There are always commercial customers, haulers, residential customers, and others looking for a convenient and cost-effective place to empty trucks.
The key to having an optimal operation is based on many factors. The six top factors to consider when thinking about building and running a successful transfer station are location, efficiency, durability, flexibility, cost, and safety.
Choosing the location of a transfer station
The location of the facility needs to be right for you and for your customers. If you own your own hauling company, your transfer station needs to be located so that your vehicles can easily get to it in terms of access roads and expressways. It also needs to be located within an area of the market that is as centrally located as possible to maximize fuel efficiency, routes, and drive time. If your own fleet of trucks is the priority, access and markets should be the primary factors in making the location decision, and third-party customers would be a secondary consideration.
Another factor could be the towns or municipalities that you are dealing with. Each one has its own way of dealing with waste disposal and recycling and will have very different ideas on what a host agreement could look like. It is very important that you have these discussions with them individually, to see who wants you there and who doesn't, how that impacts your ability to get a permit, and how it impacts you financially.
When it comes to your customers, they want a facility that is easy to get in and out of, has a quick turnaround time on-site, is cost-effective to tip at, and is safe. You should work hard to identify who your potential third-party customers are before finalizing your location so you can work with them to establish agreements early in the process, and so that they can help increase your volumes and potential revenues. This applies to your larger customers. All the smaller "one-off" contractors and residential customers will be a bonus.
Maximizing efficiency for transfer station operations
This is as simple as "get them in and get them out." Whether it's your vehicles, your third-party customers, or trucks for hauling out material, the key is to have a site designed so that you can get the vehicles in and out in 15 minutes or less. Questions to ask when designing your transfer station include:
- What are the total tons of waste received daily? Is the tipping floor the correct size to properly manage it?
- What types of materials are received and how will each one be managed most efficiently?
- Is there enough tipping floor space to handle one to two days of materials without impacting the current day's tonnage in case of weather events, strikes, or other factors that impact sending materials off-site?
- Is there on-site queuing space prior to the scales?
- How many scales and what types of weighing/tracking technology will be used for vehicles (manual or RFID)?
- Is there easy-to-read signage on-site directing people where to queue, where to tip, and where to exit?
- What is the number of tipping bays for customers, and will there be dedicated bays for various vehicles?
- What type of equipment is used to clean floors and load trailers?
- Will there be live loading of outbound trailers or pre-loading and staging?
- Can you store weights for as many vehicles as possible to limit the number of vehicles required to scale on the way out?
- How many outbound scales are on site?
It's important to take all of these factors into account and gather all of the information you can prior to designing or redesigning. It is important to work with your design/build firm to make sure you right-size your facility to properly manage all of these factors, both for the short term and to handle potential growth in the future.
Factors that contribute to the durability of a transfer station
The last thing you need to deal with when you are operating a transfer station is constant shutdowns for repairs and maintenance. There are many ways to make sure your facility is designed to handle the daily "torture" a transfer station endures, and an experienced firm that has a proven track record designing and building transfer stations can guide you through all the means and methods.
With respect to building durability into a transfer station, the top seven factors to consider include:
- Tipping floor design: the right mix design, reinforcement, thickness, and wear layer, are very important. Many tipping floors can last 15-plus years using the right mix design, and we have tested many mixes over our long history. Specialty toppings have their place in some applications, but many transfer stations don't require it.
- Push wall design: the right height, thickness, steel embeds, etc., will allow the push wall to last the life of the building.
- Building height and overhead door openings and protection: everyone is tired of repairing overhead doors. It's easy to eliminate many of these issues when the building is designed the right way the first time.
- Loading pit design: depending on the type of pit, there are many decisions that can be made to make sure it will last for the long term.
- Properly managed leachate: avoiding floor trench drains is the key. There are options for designing your transfer station with a better, easier-to-manage leachate collection system.
- Site paving: depending on your traffic counts and type, you need to evaluate what the right paving solution is for you so you don't have constant site maintenance.
- Yellow iron: Heavy equipment, such as wheel loaders operating in a transfer station, in the hands of a poorly trained or careless operator, can cause damage. Money and time should be invested to make sure your yellow iron operators know how to properly manage the material pile in the facility and load trucks in a safe, efficient, and careful manner. Otherwise, no matter how well you build the building, it will wear out quickly.
Flexibility is all about being able to adjust your operations, building, and equipment to accommodate changes in your marketplace based on the evolving material stream, customer base, and increased tonnage. You want to design a transfer facility so that you can make future changes in a way that impacts your daily operations as little as possible. These modifications could mean building additions or changes, adding scales, or many other things.
Being cognizant of the fact that the market will change, you can design your facility for this by planning the structure with expandable steel frames, and by having space on-site set aside for future expansion. You will not likely know what your future changes or growth may be, but you can come up with potential options for how the facility could grow and change over time. Be forward-thinking based on what you know today and what you have seen in the past, and use a design/build partner who has been around for a long time and is aware of the upcoming changes in regulations to help guide you through the process.
Building for your budget
A construction budget must be stuck to and an operational budget must be hit to make a transfer station a feasible long-term solution. It's important to be transparent with your design/build partner on what these budgets are so you can work together to stay within the parameters, while also accomplishing as much as possible with respect to the efficiency, durability, and flexibility of the facility.
Many factors drive construction costs that are outside of your control, such as the area where you are located, site conditions, permit requirements, type of building construction, and aesthetic requirements from local municipalities. On the flip side, many costs are controllable, and you can explore many options with the help of your contractor. It's important to do this early in the design phase so that you don't have to make changes during the design process. An experienced transfer station contractor can present many different options and costs for you to make educated decisions and help maintain your budget.
Operational costs can also be worked through during the design phase as you cover how many pieces of equipment you want to operate, how many employees you need to have, annual maintenance costs for the facility, and other such items. Make sure you put together a comprehensive list of everything you want to work through with your design/build team so you can help design the facility within these parameters.
Safety considerations for facility workers
While we have touched on five of the most important factors above, the highest overall priority should be designing a facility that is safe to operate and safe for those who pass through it each day. Safety must be at the forefront of all the decisions made above. This doesn't just cover traffic patterns, signage, parking, and employee walking paths, it also must deal with how to handle emergencies such as fires.
These plans are important to implement during the design process so you can incorporate them into your facility and have ways of dealing with events that can save your employees and your building from damage.
Utilizing the right team to walk you through the transfer station design/build process every step of the way is key in having a successful project that will serve you, your customers and employees from day one and for many years into the future.
This article was originally published in the October 2021 edition of Recycling Product News,Volume 29, Number 7. It was updated on December 4, 2023.