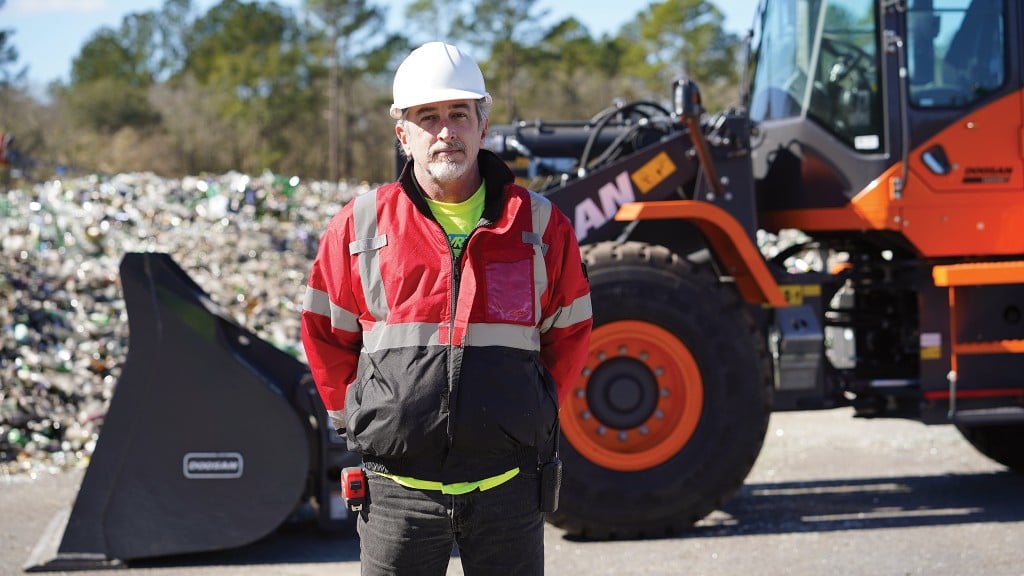
GlassWRX, an advanced technology and materials science company, is working hard to change the fact that 85 percent of all U.S. post-consumer glass ultimately ends up in landfills. Launched in early 2020, the Beaufort, South Carolina-based company's vision is a "world without waste." They take post-consumer soda-lime glass from local landfills and run it through a kilning process to create an innovative media called engineered cellular magmatic (ECM), which has many industrial applications in resilient infrastructure.
"You could say the starting point was foam glass technology, which has been around since the 1930s," explains Brad Graham, national director of site implementation at GlassWRX. "But then our founders and scientists took it to a whole new level. While ECMs are nearly 100 percent glass, they act and react nothing like the glass people expect."
According to GlassWRX, ECMs can make better, far longer-lasting and more eco-friendly concretes, and can be used to create materials that are better at cleaning polluted air and treating water. ECMs are also restorative and regenerative by design and can clean contaminated sites, or even remediate decades of nutrient and chemical pollution from the earth.
Thanks to an on-site ECM lab and test kiln, GlassWRX can also adjust inputs, cellular size, temperature and surface chemistry to custom-engineer ECMs to a customer's unique needs and specifications, whether that be in resilient construction, or for blue-green sustainable infrastructure.
Engineering ECMs requires a steady supply of glass, so GlassWRX partners with surrounding county and municipal governments to divert post-consumer glass that is too small or the wrong colour for other recycling companies from landfills back to the factory. Their Beaufort facility currently receives two to three truckloads of soda lime glass per day, which are weighed and then dumped into piles. A production supervisor checks the glass for any contaminants before moving it into production. Currently, GlassWRX processes around 135 tons of glass per day across three production lines.
A pair of loaders for purity of output
To start their production process, GlassWRX is using a Doosan DL220-5 wheel loader to load glass into a crushing machine, which cleans it with pneumatic air pressure and crushes it into pieces three-eighths of an inch or smaller. A magnetic block and trommel screen then remove any unwanted metal debris and residue. Next, a dryer ensures that the glass is dry enough to move to the ball mill, which uses 12,000 pounds of steel balls to grind the glass into a fine powder.
The powder moves along a pneumatic conveyance system to a screener that ensures the glass particles are the right size. GlassWRX then blends the approved particles into a proprietary mixture before moving the blend through a kiln process, where the mixture is heated and combined with a foaming agent to help it rise from a 1-inch layer to a 4-inch layer, similar to baking a cake. The finished product is an ECM.
To avoid any cross-contamination of raw material with the finished product, a second DL220-5 wheel loader moves the finished ECMs from the kiln to shipping preparation and storage.
"The reason we have two loaders is that even though our customers are fully aware that our product is made from glass, if they see a fleck of green, blue, clear or brown in the final product, they are going to call us because they can see glass in it," explains Graham. "Using the same machine to handle the finished product that also handles the raw feed stock would cause that contamination."
A quick coupler on GlassWRX' wheel loaders allow operators to quickly switch between attachments without leaving the cab of the machine. When ECM is ready to ship, the GlassWRX crew pairs a DL220-5 with a light-material bucket to load material into 8-foot-high, open-top containers on trailers. For ECM stored on pallets, a wheel loader outfitted with a pallet fork acts as a forklift to fill the trucks.
"ECM is 15 pounds per cubic foot - incredibly light material," Graham says. "To give you a comparison, marshmallows are 21 pounds per cubic foot. So, I ordered the biggest bucket I could get for the wheel loaders because material weight is not an issue."
"We've given ourselves extra capacity for what we can use the machines for," he continues. "We switch to the forks and use it as a forklift and then turn it right back into a loader. Each time we switch attachments using the quick coupler, it's probably a 30-minute savings compared to changing them manually."
Tailored to glass recycling
When selecting their wheel loaders for this application, GlassWRX looked for reliable parts availability, which Doosan provides via distribution centre in nearby Suwanee, Georgia. Operator comfort was another key factor in their decision. Their DL220-5 wheel loaders feature an air-ride seat and easy ability to adjust controls, specifically to enhance operator comfort.
"You can operate one of these machines for several hours and not have your back aching or your knees hurting, or all the other things that occur if the machine is not very comfortable," says Graham.
Responsive controls were also important for GlassWRX, to provide the operator with more precision when loading glass into the crusher and stacking ECM into transport trucks.
"It's almost like operating a video game joystick," he continues. "It's very easy for the operator to fall in tune with operating the machine and getting it to do what you want."
He adds that the GlassWRX facility is a busy complex, and they definitely appreciate the standard rear-view camera that enhances the operator's visibility.
"Without that camera, you'd probably risk injury to property and person, especially on a site like this where there are people around all the time," Graham says. "I can minimize the risk of property damage and see when there are people behind the machine. I think it's probably the best safety feature on the machine."
In addition, easy access points and simple maintenance checks keep their loaders' daily maintenance routines efficient, according to Graham, so he can focus most of his time on the glass recycling work. He points to easily visible lubrication points and fluid ports as two of the biggest maintenance benefits.
To further boost the efficiency of their wheel loader maintenance, GlassWRX uses DoosanCONNECT telematics. This diagnostic tool allows their crew to digitally monitor the health, location and productivity of their wheel loaders and receive alerts about maintenance notifications. The company also has plans to integrate DoosanCONNECT telematics into their larger facility monitoring system.
"Our entire facility is designed for us to monitor everything that's going on through the computer, and track maintenance events," Graham says. "Being able to hook these machines into that same system is one of the things I thought about when purchasing. So far, these machines are just perfect for how we're using them."
Laura Miller is a strategic communications specialist based out of Des Moines, Iowa. This article was submitted by Doosan Infracore North America, LLC.
This article was originally published in the September 2021 edition of Recycling Product News, Volume 29, Number 6.