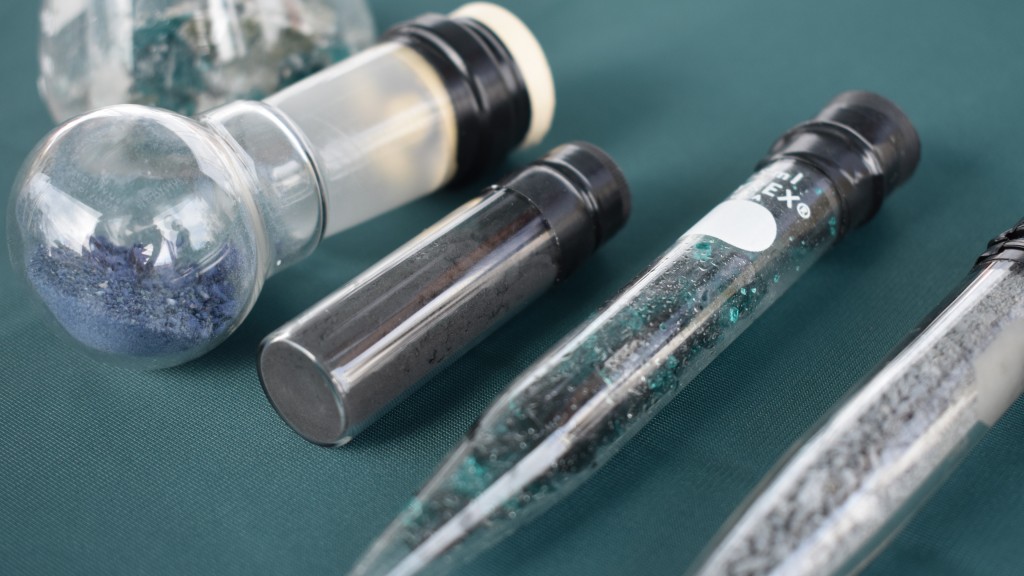
Redi-Cycle converts battery materials at a high purity to secondary materials through a hybrid solution of hydrometallurgical and electrochemical recycling, reducing mining demand and increasing end user savings. The final product is a Nickel and Cobalt metallic alloy, called Redivivus Nickel, that bypasses the challenging and costly process of separating the elements.
Redi-Cycle decouples recovered materials from battery production flow and inserts them as an alloying feedstock into metallurgical operations of the stainless steel and superalloy industries. However, Nickel and Cobalt are infinitely recyclable and can be placed back into battery production flow as cost-effective technologies develop.
As part of this trial, the PoC demonstrated a 92 percent minimum recovery rate of Nickel and Cobalt at high purity to create Redivivus Nickel. Additional elements such as Copper, Manganese, Iron and Lithium were recovered at high levels. The success of this PoC will help to further strengthen Redivivus' business advantage to drive new revenue opportunities with metallurgical consumers.