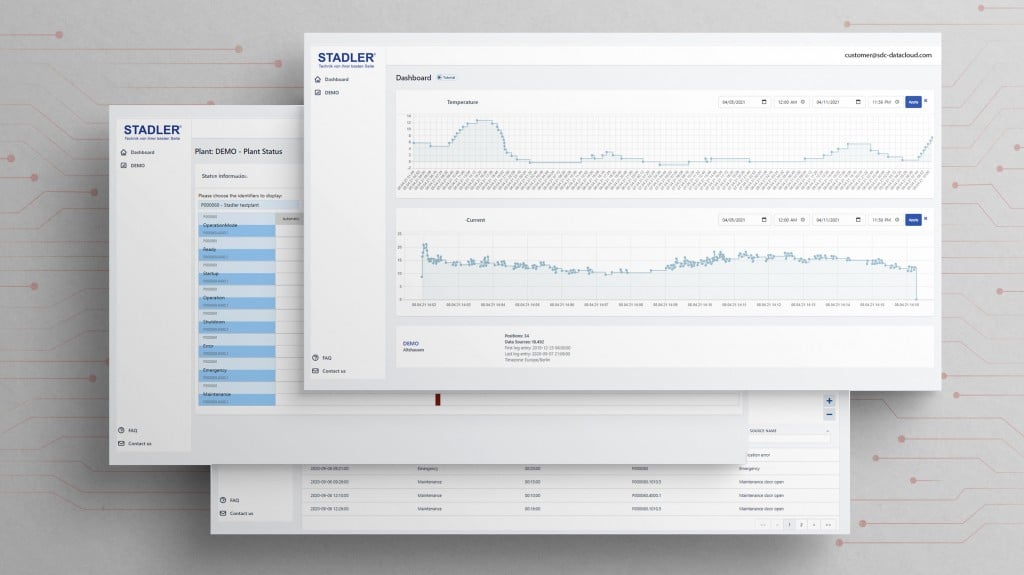
STADLER has developed an SDC cloud-based platform which captures operating and sensor data from equipment at sorting plants. The information is then securely stored in the cloud and accessible from anywhere on- or off-site through a web portal.
The SDC leverages automation and the Industrial Internet of Things (IIoT) to optimize and increase the efficiency of processes in STADLER sorting plants and provide better, faster support to its customers.
Amela Sijaric, Co-Head of the SDC Team, at STADLER says: "The SDC puts the customer and our Service Department in direct communication with the individual machines in the sorting plant. It provides valuable insights into the operation and enables us to work more effectively with our customer to resolve any issues as they arise, and to ensure that the plant continues to meet their evolving requirements effectively. The SDC is a tool with great potential, and we will continue to work with our customers to extend its capabilities with new functionalities."
SDC can also be implemented in existing plants. In these facilities, it can highlight areas where processes can be improved, and can also be used to implement updates to the existing equipment.
Optimized process efficiency, maximum uptime
The SDC provides an overview of the operation of the sorting plant, with visibility on the individual machines. The data captured by the system is a powerful tool to enhance the sorting process, identify any bottlenecks or issues and act to resolve them swiftly. Analysis of the historical data can help to optimize machine performance and reveal opportunities for improvements in the plant's efficiency.
When there is an issue, with the SDC it can be resolved faster and more efficiently. "The system flags where the error is in the sorting plant's flowchart, with a clear indication of the name of the device experiencing a fault," explains Sijaric. "The customer can see at a glance where to go to sort out the problem. If they need help with the issue, our technical experts can immediately access the machine data. They can understand the issue and provide a solution swiftly. This is particularly beneficial when the plant is a long way from STADLER Service Teams."
Full access to updated documentation and tutorials
The SDC has a section dedicated to providing customers with flexible access to a full library of documentation for each of the machines in their plant, so that it is always up to date. They include not only data sheets and operation manuals, but also a spare parts catalogue.
When making an order, the customer will easily identify the correct part with the photograph, description and part number in the catalogue. The Documentation section also offers tutorial videos prepared by the STADLER Service Team, covering the maintenance tasks typically conducted by the customer.