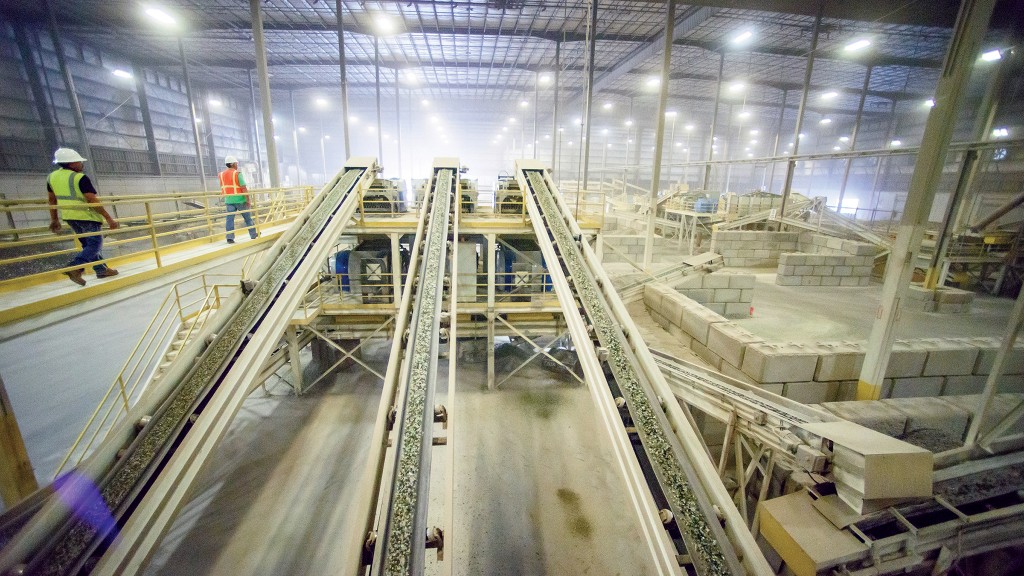
Strategic Materials is the largest dedicated glass recycling company in North America, and one of the largest in the world. The company, based out of Texas, operates close to 50 plants total, including two glass recycling plants in Brampton and Guelph, Ontario, and another plastic and film recycling plant in Brampton, Ontario.
"Comparing to other glass processors in North America, we're by far the biggest," says Curt Bucey, executive VP and chief commercial officer for Strategic Materials. "I think the next biggest on the blue box side of things might have three plants."
According to Bucey, there are not a lot of MRFs or other recyclers which are dedicated to recovering high volumes of used glass for resale in either Canada or the U.S. "The equipment required to do this is expensive and it's specialized and it takes space," he says. "Most MRFs don't have enough volume to justify doing it. We're a consolidator of smaller plants in some cases, building a big enough volume to justify putting in the expensive equipment that we use."
Behind the glass recycling process
At Strategic Materials their process for recycling glass varies between different plants, depending on the type of glass coming in from MRFs or other suppliers. Three mix is a large part of their incoming volumes (single-stream coming from curbside pickup originally) which is highly variable in quality, colour and size. "Our process is largely a function of the supply we get," explains Bucey. "Some MRFs break material down smaller, some leave it bigger, and there is lots of variability in the amount of shredded paper and other contamination mixed in. If there's not a lot of ‘policing' on what goes in the blue box, then we tend to get more contamination."
For mixed glass from single-stream collection, Strategic Materials runs it through a pre-processor. Bucey says they haven't always had to pre-process mixed material, but as contamination in their incoming stream has become increasingly significant, they needed to cut down on the variability of their input.
"The pre-processor step basically means we take a highly variable input and try to knock it down to a more controlled material. It runs through vacuums and air knives, air blowers and suction working in conjunction, and is basically the process of separating lights from heavies - largely shredded paper from ceramics."
Following the pre-processing step, they run material through robust metal sorting, screening and optical sorting by colour. He says screens are absolutely an important part of their process, at the front and middle. "We've used vibratory screens and trommel screens. Trommel screens tend to break the material. We try not to pick up and drop material, but rather shake it down the line with vibratory screens."
When they get plate glass, window glass, or other homogeneous material, it can skip the preprocessor. "We don't need to go through a preprocessor when the variability of the product is not there. If it's all clean plate or all green bottles, in some cases we don't have to run it through optical sorting because it's already clean. For plate glass, for example, we use very little optical sorting. It's just crushing, screening and removing metal contaminants."
He says where the crushing stage comes into their process also depends on the type of glass. At Strategic Materials, they use three types of crushers: hammer mills, vertical shaft crushers and roll crushers.
"You don't want a whole bottle to go through an optical sorter," continues Bucey. "So, before we hit the optical sortation, we're going through a crushing step to get pieces to the size the machines can look at. Some glass recyclers screen first and crush later, some crush first and screen later. It depends on the material."
The market price for recovered glass
When it comes to commodity prices for resaleable cullet made from recovered glass, Bucey says it varies greatly between regions. "Every region is different and the amount of distance that the material has to travel to get to an end market is different, and we have customers that will pay more for the material if it has to travel a lot further," explains Bucey. "Overall, the commodity pricing trend for glass has not been negative. The price point for our finished glass material has been pretty stable, and it's probably the most stable overall of all recyclable materials. We don't have fluctuations due to China, or the wild swings that the paper, plastic or aluminum industries have."
Bucey continues, "Glass has been relatively consistent year over year. That's one of the strong advantages of glass is that we don't see lots of disruptions in price. The price that we pay for material is probably equally stable but that's hidden a little bit.
"What has happened is that we've tied the price of glass to the amount of contamination on the inbound side. So, while the base price per glass may not have changed, the amount of garbage or contamination in there over the last 10 years has gone up. As the amount of contamination in inbound glass goes up, the end price goes down. At times, we hear people say, ‘glass pricing is negative,' but really it's not the glass pricing, it's just the amount of garbage in the glass that has gone up."
He says as far as end markets go, theirs are mostly domestic (within North America).
"We do ship material offshore and there is a demand for it. There are much higher quality standards offshore, so it's not as easy to do," he explains. "The reality is for us, the demand in Canada and the U.S. is far larger than the amount of material we have."
He says that by far their biggest end market is the container industry, and their second largest is fibreglass. Beyond those two very large markets, other end markets, including abrasives and foam glass, are relatively small.
Glass recycling advice for MRFs
According to Bucey, one of the major things many MRFs are missing is real-time measurement of their inbound material. "If a MRF is having problems with material coming in from one route or two routes, or one area of the city, they don't really have a way of knowing. The way they commonly do it is through an audit. An audit is okay for being an indicator, but an audit won't tell you that one particular area of the city is good on Monday and bad on Friday."
He says for those MRFs doing an audit once every six months, they are generally making an assumption that the day they are doing the audit is representative of all the other days in that period, but this is not necessarily accurate. Audits typically aren't done, for example, at busy times of the year like after the holidays where there can be very high variability in the stream relative to other periods.
"We measure every load coming in and we know in real-time where there's a variation," he says. "We know the difference from Supplier A and B, but we also know the variation that Supplier A has over a period of a week, month and a year."
He says real-time measurement of inbound material can help MRFs in dealing with their respective cities, as it provides a basis from which to let the city know that they are not living up to their commitment on reducing contamination at the point of collection.
In cases where a MRF is operating inefficiently, Strategic Materials can go in and help by pointing out areas where they're not being as effective as they could be.
"We have MRFs around the nation that are supplying us with 7 to 10 percent garbage, and we have other MRFs that are supplying us with 30 to 50 percent garbage," says Bucey. "In some cases, it's pretty easy to remedy. We send a guy in and he tells them what isn't working."
Sometimes, he says, MRFs don't have their glass recycling system turned on at all, or they just need to change their baghouse filters, for example. "It's the simple stuff that makes a difference, and just like with anything, there are good operators, average operators, and there are poor operators. Even a good operator can miss some things."
The price Strategic Materials pays for glass is primarily based on quality, which they measure daily. "We give every MRF we work with a matrix that says, ‘If you're at zero percent garbage and zero percent in undersized, here's your price. If you're at one percent here's your price, if you're at 30 percent here's your price,' and so on. So, they have a matrix, we show them where they are and we say, ‘If you do this and do that, you'll probably go from 30 to 25 percent, or even 20 percent, and we can show them the change in price we pay for the material.
"If a MRF is doing 1,000 tons per month and that change in price is 10 dollars per ton (as a random number) that's $10,000 times 12 months: $120,000. Then that piece of equipment that we're recommending the MRF install for $70,000 now has less than a year payback."
"Quite honestly, we can do the job with our preprocessor, but what is being missed is that we're spending money to transport mixed material from the MRFs to our plants to do something that they could be doing on site, and they could be getting a higher price for their material. Why ship garbage around? We would rather have 95 percent clean glass coming in because then our plants run better."
For Bucey, it's simply about going into a MRF and letting them know there's better systems out there, or letting them know the difference between a cheap fix and the resulting yield, compared to the more expensive fix, with its greater yield and shorter ROI.
Bucey adds that even if an operator is running a single-stream MRF without glass recovery, they are still going to have glass at the very front of their line. "You're still going to have a glass breaker and you're still going to have a screen," he says. "All materials are run through, and anything like coffee cups or other contamination will hit the crusher and then fall through a screen, out as residue. If you add glass processing in, in many cases all you have to do is beef up the screen a little bit, which does not cost a lot.
"The only time that this doesn't work is when the MRFs that are supposed to be at a certain amount of tons per hour try to flood their system by reducing the angle on their star screens. This allows contamination further down the system, and is just poor operation versus knowing what these systems are designed to do."
Glass recycling advice for cities
With respect to the collection of materials, cities should consider that the difference between a drop-off program and curbside collection is significant, and it does impact the glass recycling industry.
"There have been some cities that have looked at eliminating curbside and going to a drop-off program," he says. "We discourage that. I think part of their decision is based on the economics I talked about earlier. But MRFs and cities really need to understand the economics from our perspective.
"Drop-off programs are good for cities that don't have a curbside pickup in place, or rural areas. When a city goes from curbside to drop-off, the volume goes down by up to 99 percent. It's a huge drop-off. Could it recover over time? It grows back a little every year, but it would take forever to get back to curbside volumes. Where curbside pickup is already in existence, I support keeping it."
Bucey adds that they also hear stories about cities taking glass out of their recycling stream entirely, and in most cases, it's done because the city decision-makers haven't reached out and tried to really understand the big picture with respect to glass recycling.
If cities decide to go this route, Bucey says "Typically, their phone starts ringing like crazy from citizens asking why they can't recycle their glass." In one recent survey, they found that basically in every category that was measured, glass has the highest positive rating by consumers for recycling of any material.
He emphasizes that one of the messages he's working to spread to decision-makers is that if they are thinking of altering their glass recycling program, they should reach out to a glass recycler first. Cities, counties and municipalities should verify their information, and not count on information from third parties. "They should reach directly out and ask to have some discussions with an established glass recycler to get a balanced explanation about what is going on in the industry, and then make the decision."
Bucey estimates that in 90 percent of incidences when a city does decide to cancel their glass recycling program, they're making a decision based on faulty information, which may or may not have been passed around from city to city.
"Decision-makers need to reach out further down the supply chain and understand directly from glass processors what their needs and challenges are. Could they use more material? If they reach out to the glass container industry, or to the fibreglass industry, all of them are going to say, ‘we don't want less material, we want more."" RPN
This Editor's byline first appeared in the January/February 2021 edition of Recycling Product News, Volume 29, Number 1.