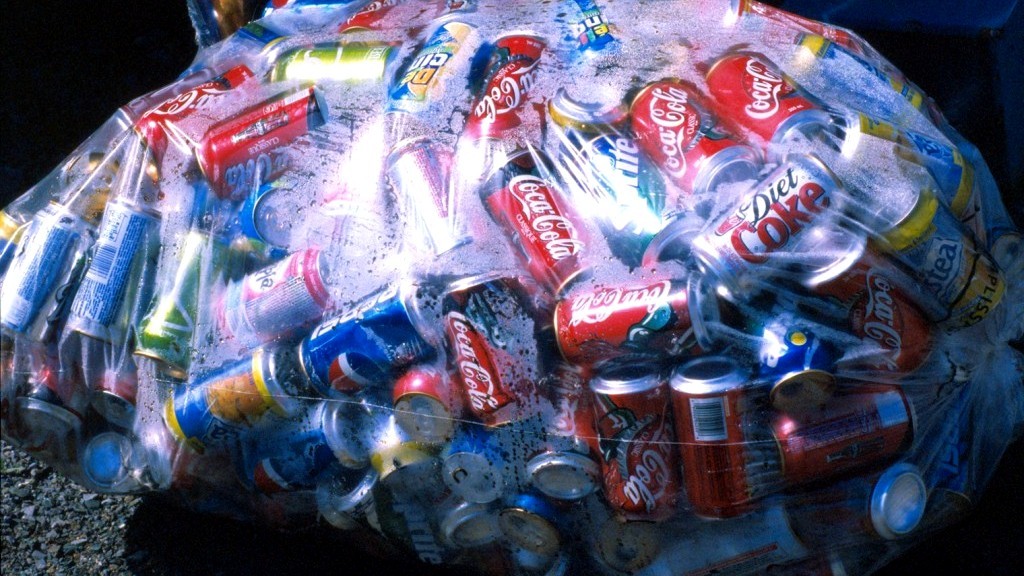
Harsco Corporation's subsidiary ALTEK is now able to provide complete end-to-end dross processing and environmental solutions to enable the global aluminum industry to maximize aluminum recoveries and achieve zero waste.
In May 2018, Harsco acquired ALTEK to expand the metal recovery by-product reuse capabilities of its environmental division, Harsco Environmental, into the aluminum industry.
"ALTEK is providing modern solutions to age-old problems, drastically reducing atmospheric pollution and pushing the aluminum industry to a zero-waste scenario through sustainable methods of producing aluminum," said Ian Johns, managing director of ALTEK. "Our latest technology is designed with Industry 4.0 in mind, driving the digital transformation."
The cost-efficient recovery of metal and other valuable materials - and environmentally safe solutions for residual waste materials - is increasingly important to the aluminum industry.
"Every cast house is an opportunity for innovation, and we are delivering end-to-end solutions that improve cast house operations, including aluminum dross processing systems," said James Herbert, global sales director of ALTEK. "The result is the best range of technology available to reduce dross generation, maximize aluminum dross recovery, improve efficiencies, and provide significant environmental and recycling benefits. As we hold a deep understanding of the process, we are also uniquely equipped to find solutions to customer problems and customize our variety of offerings to meet customer requirements."
ALTEK is the first provider of a commercially viable and fully scalable in-house salt slag recycling solution available to the aluminum industry. The AluSalt salt slag processing technology enables aluminum producers to recycle metallics and salts, recover other non-metallic products (NMPs) and achieve zero waste, addressing one of the largest environmental concerns within the aluminum market.