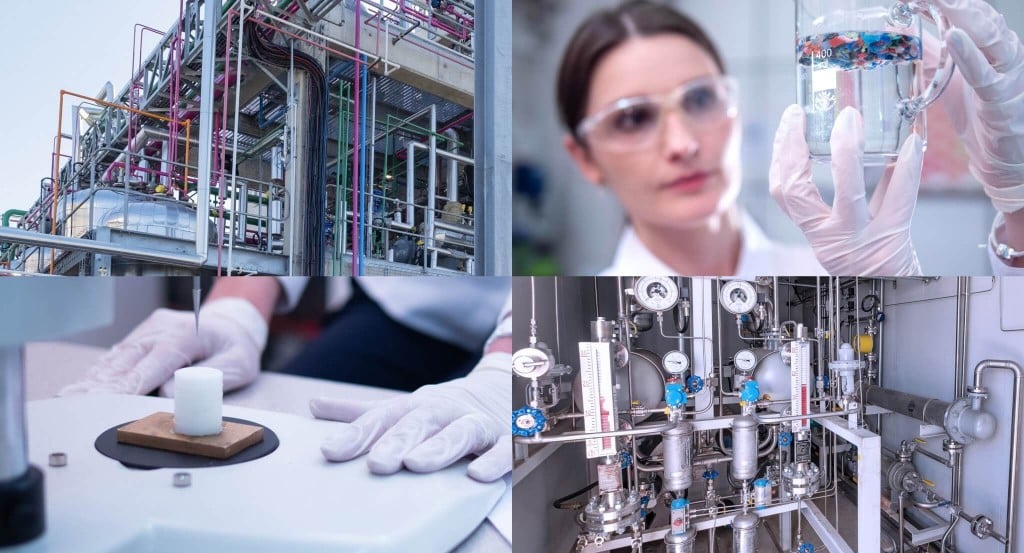
Clariter's unique plastic recycling solution has achieved a net negative carbon footprint according to the results of a new study, meaning it does not add to, but rather depletes carbon from the planet.
The results stem from an independent initial Life Cycle Analysis (LCA) carried out by CE Delft, a research and consultancy firm. The LCA determined that Clariter's carbon footprint is below zero indicating a net environmental benefit, with the solution actually reducing carbon emissions.
Unlike the majority of the recycling industry which focuses on recycling plastic waste mechanically, Clariter recycles chemically. As a result, the innovative technology transforms unwanted plastic waste into high-value, ready-to-use pure industrial products, thereby providing a breakthrough solution for the plastic waste epidemic. Clariter complements mechanical recycling by upcycling plastic waste streams that cannot be processed mechanically. The company's patented 3-step chemical process results in the upcycling of plastic waste into sulphur-free, odourless, and pure chemicals: aliphatic solvents, white mineral oils, and paraffinic snow-white waxes. These are further used as ingredients for more than 1000 end- and consumer products.
Clariter's near-term plan is to build and operate full-scale plants, each of which will recycle 60,000 tons of plastic waste and produce 50,000 tons of clean products annually. The LCA study also highlighted that the Clariter process offers significant benefits for the treatment of plastic waste that cannot be recycled mechanically. Geert Bergsma, Manager Supply Chain Analysis, CE-Delft said: "CE Delft performed a life cycle assessment for Clariter, from cradle-to-gate. The results indicate that their solution looks more attractive than alternative, non-mechanical recycling polyolefin disposal routes and an even stronger CO₂ negative footprint is well within reach. If fully renewable utilities are used, this statement can be made even more so."
When comparing the recycling of plastic waste (polyolefins) by Clariter, with other waste treatment routes for polyolefins, the outcome includes both the impact of the production processes and the environmental benefits of avoiding conventional products or energy. The LCA results prove that:
1. Clariter's carbon footprint is negative (below zero), which indicates a net environmental benefit. Compared to others, Clariter is not polluting or depleting but rather cleaning the planet.
2. The impact and benefits of Clariter's solution supersede those of the pyrolysis process, which produces intermediates, e.g. energy, fuel, or new plastics. The pyrolysis process prolongs the life of plastics, whereas Clariter ends it for good.
3. Clariter's Full-scale Plants are expected to show favourable energy generation to that of incineration in Municipal Solid Waste Incineration (MSWI). It is also expected that they will be competitive against best-case pyrolysis processes, as Clariter's solution has a lower carbon footprint.
Petra Koselka, Clariter COO, said: "Being net carbon negative is a unique and strong position. With further optimization of our plants, and using renewable energy sources and possibly green hydrogen in the future, we expect Clariter's process to have an even more advantageous carbon footprint. Delivering such green products to our customers - offering the industry "a clean slate" - is at the heart of what we do. The outcome is not only an important step for us but the entire chemical recycling sector."