How sustainability in the manufacturing process can help close the loop in the supply chain
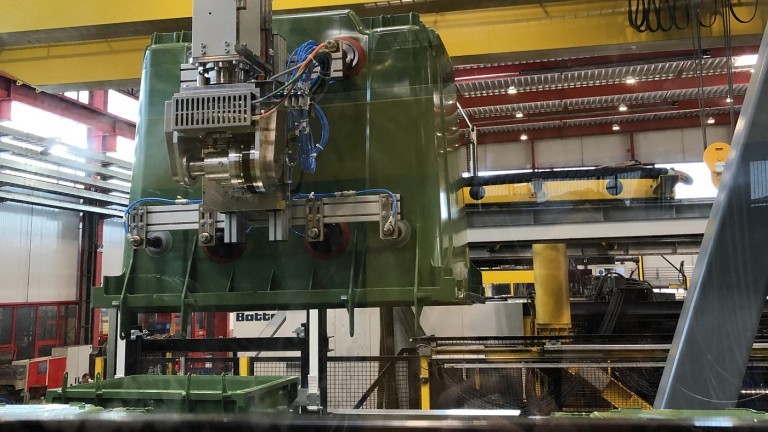
While there's lots of noise in the worldwide media about plastic taxes, recycling, consumer responsibility, and so on, there's one fundamental element which lies at the heart of all this - the desire to create a more circular and less linear economy.
Peter Vernon, MD at intelligent waste storage solutions firm ESE World, explores why the circular mindset needs to be in place during the design and manufacturing process, plus the role high-quality materials play in making this a reality.
Closing the sustainability loop
No matter where in the world, each nation is fighting its own personal waste and recycling battles. Some countries have the infrastructure to recycle more end-of-life commodities, while others are in their nascent stages and are sending many streams to landfill, or overseas for reprocessing.
However, no matter where a country sits on the environmental scale, when it comes to the manufacturing of plastic-based products - whether that be drinks bottles, car parts or wheelie bins - considering quality over solely price, can help to close the sustainability loop and promote greater resource efficiency.
Taking wheelie bins as an example, to be able to withstand the day-to-day exposure to extreme loads and regular handling by people and rubbish trucks, they must be durable and reliable - not only because their movable parts are put under strain by heavy loads, but also because if there was an accident and the container fell out of the lifting device, this could be extremely dangerous for the operative.
In truth, making products which are built to last isn't just beneficial for the environment - from a reducing waste levels perspective - or health and safety standards, it's also advantageous for a business's bottom line.
Naturally, the higher quality the material used in the manufacturing process - especially in the case of higher-value items such as waste containers - the greater the product's overall lifespan. So this means that organizations should, in theory, have lower long-term expenditure, as they won't have to buy frequent replacements.
In light of this, how much of a role does recycled material play in holding the key to a ‘greener' procurement and waste management strategy?
Embracing recycled commodities
Recycled plastic has been something of a big topic in industry in recent years, and this doesn't look likely to change any time soon.
An increasing number of companies are joining plastic pacts, more states and countries are banning plastic bags, and the UK has set the wheels in motion for a plastic packaging tax - all of which are signs that a metaphorical storm is breaking, and people are doing more to try and help protect our planet's resources.
So, when it comes to manufacturing, recycled materials shouldn't be overlooked.
There's been lots in the news this year about oil prices plummeting and the subsequent effect this has had on the virgin plastic market, which has naturally led to fears that this could negatively impact the sustainability agenda.
But regardless of the price in financial terms, it's vital that considerations are given to the ‘cost' that less ethical decisions have on the environment - including increased carbon emissions, higher landfill volumes and depleting resources, to name just a few.
The fact that our world's resources are running out should be a wake-up call to industry, to make people reconsider the "way it's always been done" and see if there's an eco-friendlier alternative. Because at the end of the day, it's by making more conscious choices during the procurement process that businesses, councils and individuals have the power to influence new habits and a more sustainable future.
We can put this into context by looking at HDPE - a material commonly used in the manufacturing of plastic products. The energy consumed in the production of recycled HDPE is 12% of that required to process its virgin counterpart, and the overall environmental impact from producing recycled HDPE - as a CO2-emission-output equivalent - is 35% that of virgin.
Making eco-conscious choices
It's figures like these that quantify our decisions, but there are also many other certifications and ecolabels businesses and councils can look out for, to ensure they're buying the most sustainable products.
For instance, German ecolabel ‘The Blue Angel', is one which sets high environmental standards for product design - looking at longevity, ethical sourcing of materials and low pollution impact. Ultimately, this accreditation empowers people to understand where goods come from and their closed loop life - which often inevitably influences their purchase.
Under ‘The Blue Angel' standard, plastic wheelie bins for example the share of post-consumer resin (PCR) in the plastics must be minimum 80%. And if more manufacturers strived to comply with such labels, this would have the potential to reduce our consumption of virgin plastics - a huge opportunity given that the world produces around 381 million tonnes of plastic waste every year.
There's no denying that the road to a truly closed loop future will continue to have its challenges, but by ensuring the material in the manufacturing process is sourced sustainably and has a low carbon footprint, the more positive the impact will likely be on the wider supply chain - creating a network of producers and consumers who want to help to save the planet from collapse.