CarbonLITE begins production at world's largest standalone bottle-to-bottle recycling facility
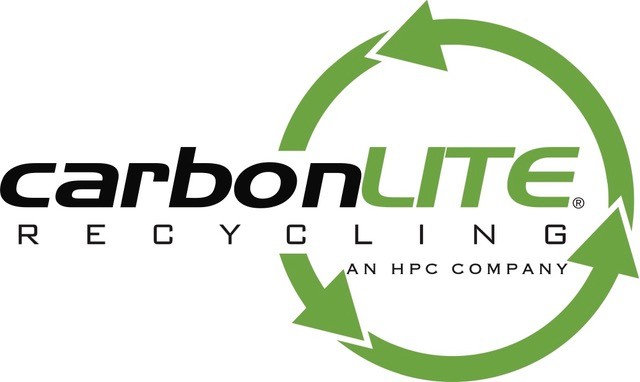
CarbonLITE has begun production at its Reading, PA plant, the largest standalone bottle-to-bottle recycling facility in the world. The plant will eventually process 140 million pounds of post-consumer PET annually, enough to process 2.5 billion rPET bottles.
The $80 million, 270,000 square-foot Reading plant, about 30 miles from Allentown in Eastern Pennsylvania, is outfitted with advanced robotic systems. It will ultimately generate 90 million pounds of food-grade rPET pellets each year.
"Even with the pandemic and this spring's constraints on recycling and industrial supply chains, we pushed forward so that we can help our customers expeditiously fulfill their growing commitments to recycled-plastic use," said CarbonLITE CEO Leon Farahnik. "We are proud to continue to help advance closed-loop, bottle-to-bottle recycling and a circular economy in a significant way."
All of CarbonLITE's long-standing customers, all of whom use substantial amounts of rPET in their beverage bottles, have facilities in Allentown. These include Nestle Waters North America, Coca-Cola, Keurig Dr Pepper, PepsiCo and other global beverage brands. By enabling these companies to avoid the use of virgin plastic produced from petroleum, the new facility is expected to prevent the release of over 60,000 tons of carbon emissions annually. CarbonLITE also provides rPET produced from ocean-bound plastic waste for the new ZenWTR premium water bottles, a first in the industry, and for all types of PET packaging, thereby further helping to rid the marine environment of plastic pollution.
Company info
10250 Constellation Blvd, Suite 2820
Los Angeles, CA
US, 90067
Website:
carbonliterecycling.com