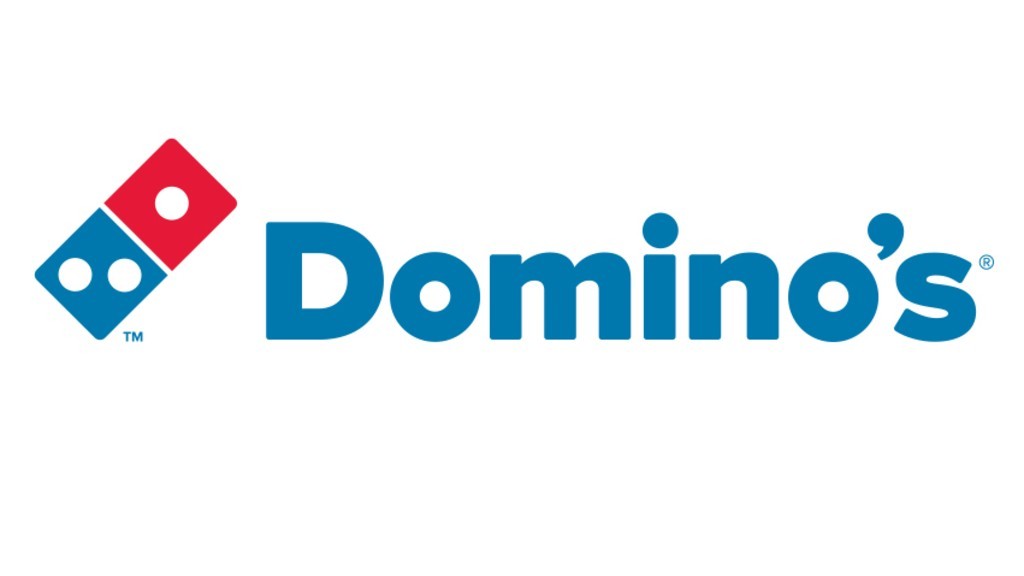
Domino's and its primary box supplier, WestRock, are launching recycling.dominos.com - a website to share the facts about pizza box recycling. The website is a hub of information on pizza box recycling, including instructions on how to recycle pizza boxes, and a guide for what to do if a customer's community does not accept pizza boxes for recycling.
Contrary to popular belief, pizza boxes are recyclable, even if they have some grease on them. To reduce confusion and encourage Americans to recycle their pizza boxes, WestRock conducted a research study that evaluated the impact of typical amounts of grease and residual cheese. The study was reviewed by member companies of the American Forest & Paper Association. It concluded that the presence of typical amounts of grease and residual cheese does not affect the quality of finished corrugated product containing expected levels of recovered fibers.
"Because nearly everything that leaves a Domino's store leaves in a corrugated box, we know we have an opportunity to make a difference when it comes to packaging and recycling," said Tim McIntyre, Domino's executive vice president of communications. "Our goal is that our customers will set aside any misconceptions they have around the recyclability of pizza boxes, read the facts and put their empty box in the recycling bin - or call their municipality and ask them to add pizza boxes to their collection."
A total of 73% of the U.S. population is estimated to have recycling programs available for pizza boxes, according to a Resource Recycling Systems access study commissioned by WestRock in fall 2019. While 27% of the population is served by programs with explicit acceptance of pizza boxes, 46% of the population has access to programs that imply, but don't say specifically, that they accept pizza boxes. The remainder are either unclear or say they cannot take pizza boxes.