STADLER separator producing high-purity plastic flakes, increasing productivity at PET sorting plant
German company RCS chose a STADLER ballistic separator to help separate clear PET from colour PET
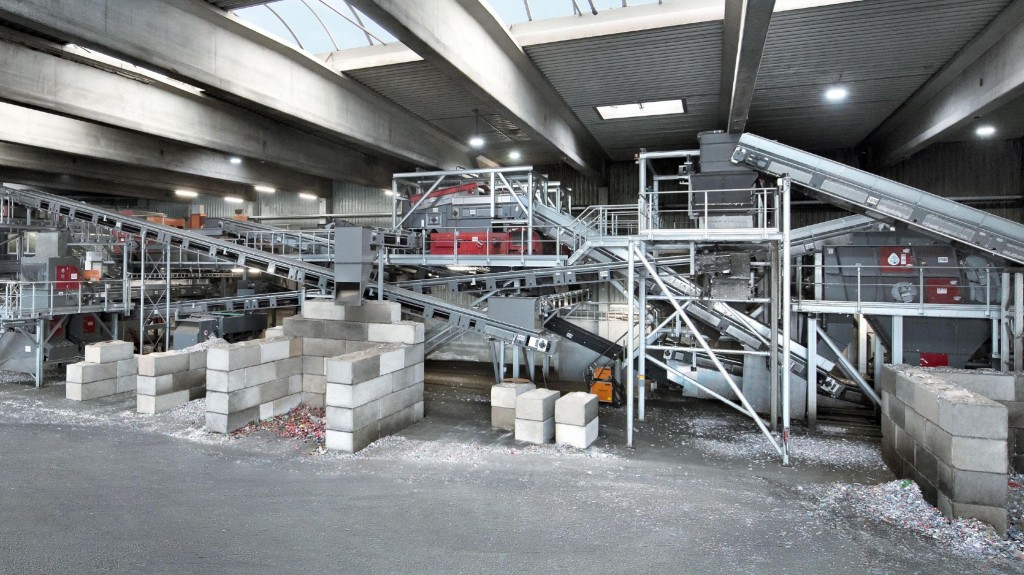
RCS is a company based in Werne, Germany, specializing in recycling management. With over 40 years' experience, it provides companies with sustainable solutions for the disposal of commercial waste with its three core competencies - waste disposal, raw material recycling and plastics.
Sustainability and the environmentally friendly use of resources are the principles at the heart of RCS's corporate philosophy. They run through every aspect of its operation, such as the advanced processes it uses to collect and transform waste into secondary raw materials, returning them to the production cycle. These core values also form the basis for its service to clients, as it works in partnership with them to develop a concept that is environmentally friendly and individually tailored to their needs.
An important area of focus for RCS is the recycling of PET bottles to produce plastic flakes for a variety of applications and high-quality regranulate for the food sector. This activity is centered at its sorting plant, where it separates clear PET from color PET - which account for 85 percent of the input - aluminum and ferrous cans, film and other materials. With a capacity of 7 tonnes/hour, the plant operates on a continuous shift system, processing used PET bottles into high-quality food grade plastic flakes.
The purity of the flakes is of paramount importance, as they are destined to the production of a variety of plastic products, from plastic fibers to films and packaging tapes, as well as products for the food industry. Every outgoing Big Bag is carefully checked for residual moisture, bulk density, incorrect colors and contaminants, as well as grain size distribution and adhesive residues to ensure the quality of the output.
A complete modernization delivers high quality and operating efficiency
In order to achieve both the consistent high purity it requires and optimize the processes at its plant, RCS has relied on STADLER over the years: "We had already purchased a ballistic separator from STADLER in 2005," says Gerd Francke, joint CEO of RCS. "On the basis of the good experience with their technology, we decided again to choose STADLER for a new ballistic separator in 2014."
This was followed by a complete modernization of the plant in 2017: "STADLER offered us the complete package, from project planning to the construction of the modernization of the entire plant, managed and implemented by their staff," explains Alexander Rimmer, joint CEO of the company. "We particularly appreciated their technical know-how and the support during the entire project. Their advice was flawless and they offered us great technical experts who advised not only on the technology and processes, but also on the implementation possibilities specifically adapted to our technical requirements with good solutions to problems."
The completion of the project within very tight deadlines was a key requirement for RCS, and STADLER delivered on this important demand: "What particularly convinced us was that they followed our tight schedule and were able to meet our expectations," adds Alexander Rimmer.
The modernization has brought multiple benefits to the sorting plant - not only on the quality of the output, but also on its operation and running costs, to the satisfaction of RCS's CEOs: "The biggest advantage was a triple increase in quantity, quality, and yield. In addition, work processes have become easier for our employees. Also, the STADLER equipment is very durable, and therefore requires less maintenance. As a result of the modernization and the simplified maintenance, costs and workflows could be optimized."
A further upgrade with a Label Remover to meet evolving requirements
The recycling industry is in constant evolution, as the packaging used by manufacturers changes over time. This is the case of PET bottles, which are increasingly packed in "full-body" sleeves: "To optimize sorting and achieve better quality for our customers, the separation of label and PET bottle must take place before sorting," explains RCS's CEO.
Once again, RCS turned to STADLER for a solution to this new requirement: "with the STADLER Label Remover the labels are stripped off and the PET bottles are less damaged than with other manufacturers. As a result, we can register less fine abrasion," concludes Alexander Rimmer.
STADLER's Label Remover - launched in 2019 with the name Delabeler - removes labels from bottles of all types, achieving a quality standard of up to 80 percent of labels removed. It processes a mass flow of up to 9 Tn/h - depending on the particle size and material composition. It stands out for the robust construction that is the hallmark of STADLER equipment and is highly resistant to impurities. These features result in excellent durability and a consistently high performance throughout its long life cycle.
The STADLER Label Remover has been in operation at the RCS PET sorting plant, where it has proved to be an effective solution: "We are very satisfied with the Label Remover because it requires less maintenance and its throughput is geared to that of our plant. With this machine, there is less wear on the knives and the machine is not very susceptible to impurities such as foil or wood. In addition, it does not cause any damage to the PET bottles. With the Label Remover, we can separate the labels from the bottles before sorting, which enables us to guarantee a consistently high level of purity," concludes Alexander Rimmer.