Maximizing metal removal in rubber tire recycling
Combatting contamination in recycled rubber using magnetic separation at critical points in the process
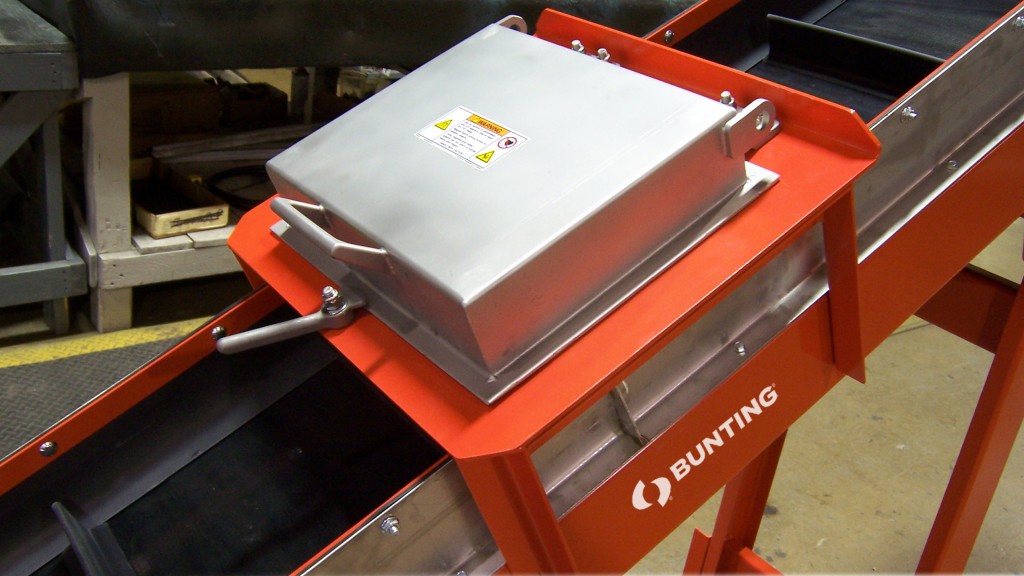
To combat metal contamination and ensure the purest recycled rubber product possible, several different types of magnetic separation equipment can be installed at critical points in the recycling process.
Recycled rubber from tires finds its way into many places. Playgrounds are one of the most iconic places recycled tire rubber is used, in the form of either rubber mats or shredded rubber "mulch." Recycled tire rubber is also used in livestock fencing, as a gravel substitute, and in consumer items such as anti-fatigue and welcome mats.
Recycled tire rubber provides a cushioned, bouncy surface, but if rogue metal contamination remains in recycled tire rubber material, the consequences can be severe.
The greatest challenge when removing metal, such as steel wire, from shredded tires is to maximize the amount of metal separated while minimizing the amount of good rubber product loss. The best way to achieve this is through multi-stage magnetic separation.
Below is a graphic depicting the typical layout of a rubber tire recycling system. Here, the primary objective is to free rubber from metal, which is usually achieved through the use of a 2-stage shredding setup. Using this method results in optimum size reduction, in addition to producing a well liberated rubber crumb material. After the second stage of shredding is complete, the focus can then turn to separation of steel.
Step One: Primary Magnetic Separation after the 2nd Shredder
During this stage, the key objective is to separate the bulk of metal from the rubber. To accomplish this, a high strength Crossbelt Magnet is suspended across a conveyor or a vibratory pan which fluidizes the rubber in order to attract, lift, and remove the liberated metal wire contamination from the rubber being conveyed.
Bunting Magnetics' Crossbelt Magnet is equipped with a tough urethane belt to minimize the risk of any wires sticking into the belt material. Bunting offers electromagnetic, permanent ceramic, and neodymium magnet design options for the overhead Crossbelt Magnet.
Step Two: Magnetic Separation of the Separated Metal Fraction
Inevitably, clean rubber product will be carried over into separated metal fraction. This material may then have to be shredded down to a finer consistency in order to liberate more wires and then be passed over a high-strength rare earth magnetic separator in a rotary design. There are several options for this kind of magnetic separator, including:
High Intensity Separation Conveyor
Stainless Steel Separation Conveyor
All of these equipment options incorporate powerful rare earth magnets into their design. It is essential that the design of a magnetic separator features an axial alternating polarity magnetic field design (a magnetic field that runs across the width of the magnetic separator), as this causes the material to tumble and release entrapped rubber as it rotates around a magnetic drum, for example.
If a drum magnet is being used, it is recommended that either a manganese steel shell or wear cover is incorporated into the design as the strong magnetic characteristics of the steel wear can lead to heavy wear over time. Bunting's engineering team will work with you to incorporate custom design choices such as these to ensure your equipment will achieve optimum performance in your process.
Step 3: Secondary Magnetic Separation
A clean, metal-free rubber product is vital. To accomplish this, second-stage magnetic separation is recommended. Second stage magnetic separation removes any stubborn metal that may have been left behind after the first stage of separation.
Recently, High Intensity Magnetic Separation Conveyors have been found to deliver excellent results in rubber recycling applications. A vibratory feeder feeds rubber crumb onto a high intensity magnetic field of the head pulley, pulling out tiny wires that may still be embedded in the crumb rubber material. This results in an extremely pure product.
Separators used at this stage of the process include:
Step 4: Magnetic Treatment of Rubber Powder
Often, recycled rubber is processed into a powdered form. When this fine rubber material is fed onto a powder grinder, a final stage magnetic separator is required in order to remove small fragments of wire and other tiny contaminant particles.
Since the volume of the metal is low at this stage of the process, a manual-clean Rare Earth Plate Magnet suspended close to the product over the conveyor or conveying it over another High Intensity Separation Conveyor is highly efficient at lifting and removing contaminant particles such as fine wires.
Effective Conveying of Tire Wire
One of the more difficult challenges in tire recycling is determining the best way to convey separated out tire wires to dumpsters. Recently, Bunting has found the most effective way is by utilizing the company's magnetic, beltless Mag-Slide Conveyors. Mag-Slide Conveyors have no moving belts, and instead use internal moving magnets to pull clumps of wires up the conveyor's stainless steel slider bed, carrying them up and into a dumpster. This is now becoming the most effective and efficient way to convey wire in a facility.
Bunting has conducted work and designed custom equipment for tire rubber recyclers around the world. While each plant is unique and the process may have different flow patterns, the company says they have developed the four steps above as a guideline for tire rubber recyclers who are interested in implementing magnetic separation solutions into each step of their operations.