Volvo CE manufacturing site in Pennsylvania is sending zero waste to landfill
All waste generated on Volvo's manufacturing campus is recycled, composted or converted to electricity
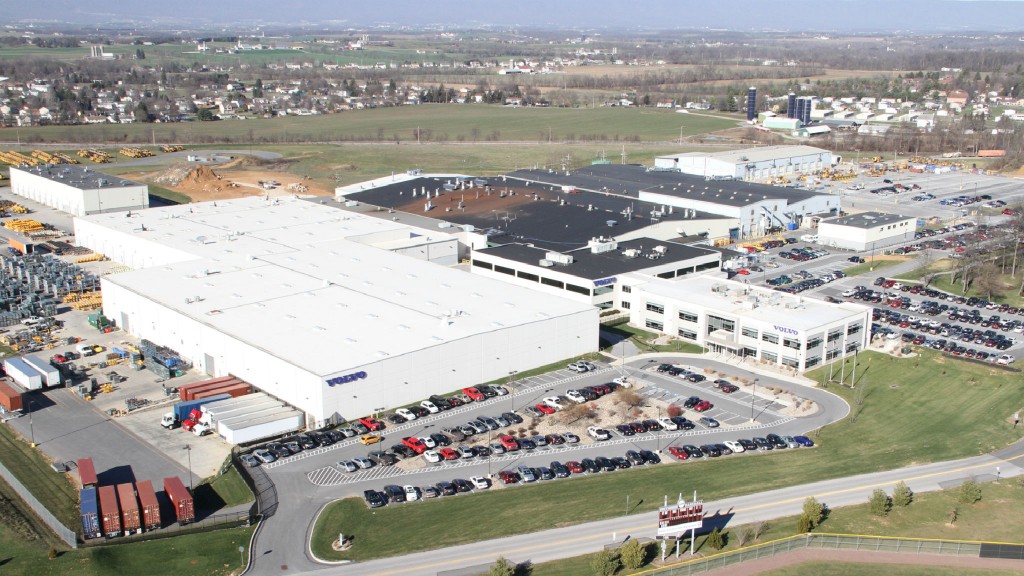
The Volvo Construction Equipment site in Shippensburg, Pennsylvania, has achieved zero landfill status. The North American campus is only the second Volvo CE location worldwide to earn this designation, which is certified by Volvo Group. The first one is in Braas, in southern Sweden.
All waste generated is now recycled, composted or converted to electricity. This includes day-to-day manufacturing and assembly operations, as well as office activities, preventive and reactive maintenance of equipment and facility systems and its on-site cafeteria.
Volvo CE Shippensburg consists of seven stand-alone buildings on 192 acres, with a total area of 838,342 ft2 under roof. The site employs over 800 people.
The journey to zero landfill was a multi-year, multi-step process in partnership with Waste Management, the site's waste service provider.
In six years, the site saw its waste handling costs slashed by over 50 per cent. In 2019 alone, the site recycled 1,171 tons of cardboard, paper, wood, scrap metals and plastics. These efforts equate to saving:
- 4,248 mature trees or,
- 3,323,689 kWh of electricity, enough power to fulfill the annual electric needs of 318 homes or,
- 3,757 tons of greenhouse gas emissions or,
- 769,300 gallons of water, enough to meet the daily fresh water needs of 10,257 people.
In 2012, office and shop floor areas began single-stream recycling. By 2016, the site had implemented composting of pre-kitchen waste, wood pallet recycling, plastic foam and rubber scrap recycling and eliminated one trash compactor that was designated for landfill disposal. In 2017, all buildings and offices transitioned to multi-stream recycling. Landfill waste began shifting to a Waste to Energy (W2E) facility in York, Pennsylvania, where it is incinerated at high temperatures, producing steam that then powers turbines to produce electricity. By the end of 2018, all waste was fully diverted from landfills.
To put the site's achievement in perspective, in 2017, 52 per cent of the U.S. municipal solid waste was still being diverted to landfill versus recycled or converted to energy, according to the U.S. Environmental Protection Agency.