Creating a better battery for end-of-life recycling
Improving battery recycling requires better battery chemistry and processes
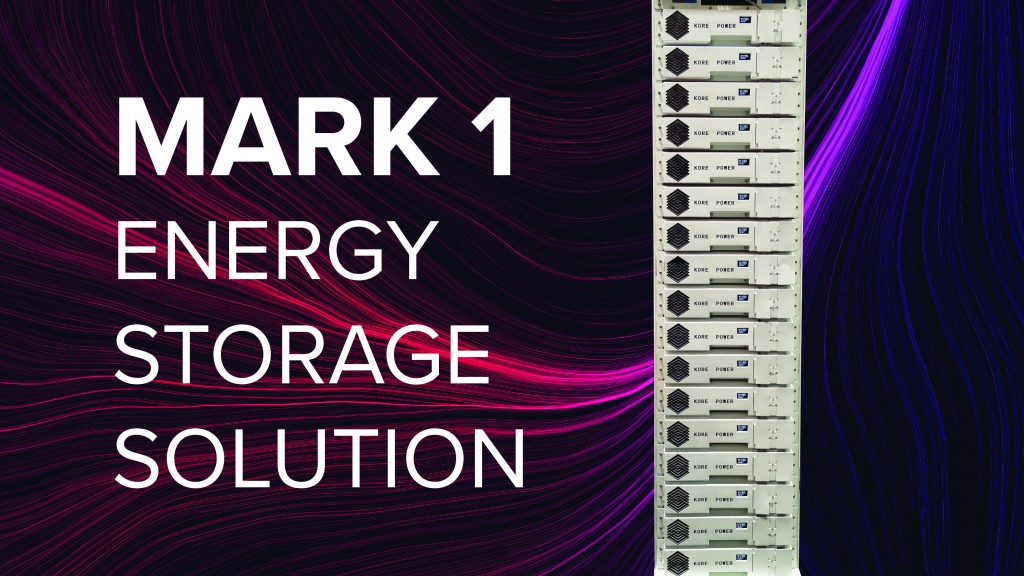
As a key aspect of the global sustainability effort, lithium-ion battery recycling has become an area of focus for many battery manufacturers, recyclers and end-users. Currently, enhancements to battery cell design and the recycling process itself are creating new avenues to minimize the environmental impact of energy storage manufacturing, deployment and recovery in a cost-efficient way.
Creating chemistries designed for enhanced recycling
As a frontrunner for industrial-grade energy storage, lithium-ion batteries offer a variety of options, each with their own unique chemistry suited for a variety of applications. The capabilities may vary but most lithium-ion batteries will fall into one of five compositional categories: Lithium-Iron-Phosphate (LFP) and Nickel-Manganese-Cobalt (NMC), Lithium Cobalt Oxide (LCO), Lithium Manganese Spinel (LMO) and Lithium Nickel Cobalt Aluminum Oxide (NCA). Within each of these five categories, the ratio of materials used can vary as manufacturers make adjustments to enhance efficiency, density and cycle life. This wide range of chemistries and components makes navigating the recycling process even more difficult.
Cost and efficiency of the battery recycling process, used for each of these chemistries, varies dramatically but the end goal remains the same — to ensure processing, transportation and labor costs do not far exceed the value of the recoverable and recyclable elements.
In lithium-ion batteries, elements used such as cobalt, nickel, lithium, manganese, copper and aluminum are considered to be valuable and worthy of recycling. Chemical compositions in batteries that include great quantities of these materials, such as LCO, NMC and NCA, become good selections.
Creating residual value in the battery itself from the start is just the first step in implementing stronger global recycling practices. However, other changes must be made in the process to foster wide-scale adoption of frequent and more effective recycling on a much larger scale.
Making the recycling process easier for end-users
Historically there has been a barrier for industrial-grade battery recycling as lithium-ion batteries used for applications such as microgrids, wind + storage or solar + storage applications, have far more implications to consider than their consumer-focused counterparts. Industrial-grade batteries are larger in both size and weight, are required to meet stringent charge and discharge demands, contain a greater quantity of hazardous chemicals, and are often dispersed or located in remote areas. Each of these factors makes the identification and transportation of end-of-life industrial batteries expensive.
In addition to introducing sustainable "design for recycling" practices into the manufacturing process with new chemistries, more manufacturers are creating built in-plans and strategies, through partnerships, to simplify the actual execution of end-of-life recycling of their products. Partnering with recycling experts and companies helps to maintain the delicate balance of focusing on the development of high density, high power batteries, while relying on an expert to manage the disposal, extraction and reuse of battery materials.
Currently, these more advanced manufacturers and their recycling partners are developing new platforms and technologies to further simplify the process of recycling battery materials. They are also creating a proactive approach to identifying end-of-life batteries that can be recycled.
And with the advent of the cloud, many end users will have remote access to and understanding of their lithium-ion batteries in the field. Using this technology, manufacturers can identify batteries that need to be replaced for degradation purposes and can alert recycling partners to collect and replace the cell.
New efforts to design battery chemistries geared towards recycling efforts are making it easier and more realistic for end users to adopt these practices and reuse select materials in next generation energy storage systems.
Combining advanced chemistries with the modernization of the battery recycling process will simplify and advance both battery selection and their end-of-life management.
Lindsay Gorrill is CEO of KORE Power , based in Coeur d'Alene, Idaho. KORE Power is a leading developer of high density, high voltage energy storage solutions for global utility, industrial and mission-critical markets.
KORE Power designs and manufactures the industry-leading, 1500V Mark 1 Energy Storage System. Developed to lower installation and operation costs with higher efficiency, the Mark 1 includes proprietary NMC cells and modules, with innovative safety features, managed and optimized by the Mark 1 BMS.
KORE Power is currently developing plans to build a lithium-ion battery manufacturing facility in North America. This facility will serve the growing demand for end-of-life battery management in applications such as fossil fuel peaker plants, wind and solar plus storage projects, Microgrid optimization, behind-the-meter C&I, E-Mobility, mining energy solutions and the military.
Company info
1875 N. Lakewood Dr, Suite 200
Coeur d'Alene, ID
US, 83814
Website:
korepower.com
Phone number:
(208) 904-1642