Pilot project from BASF to improve traceability of recycled plastics
Platform combines the power of blockchain with digital badge and loop count technology
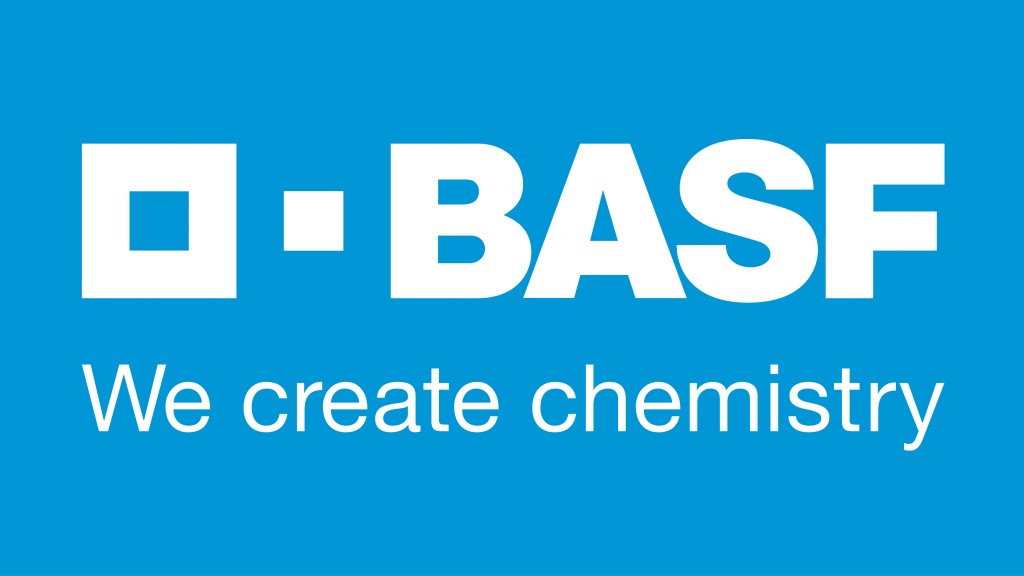
BASF has launched a pilot project called reciChain in British Columbia designed to better manage plastic waste. According to BASF, the project will introduce a more sustainable alternative to the linear economic model, reducing plastic waste, maximizing its value and enhancing resource efficiency.
According to a report produced by Deloitte for Environment and Climate Change Canada, Canada disposed of nearly 3.3 million tons of plastic waste in 2016. Of these plastics, less than 11 per cent were recycled, meaning the rest were landfilled or lost to the environment. If the present trend continues, the report estimates that Canadians will dispose of $11.1 billion worth of plastic materials each year by 2030.
"There is a clear global challenge around the economics of recycling plastic. Much of the collection and sorting activities are challenged by manual processes and material contamination. Additionally, traceability is a concern as new commitments start to emerge from brand owners and retailers," said Marcelo Lu, President, BASF Canada. "With reciChain, our goal is to revitalize the value of plastics and significantly improve circularity in the supply chain."
The platform combines the power of blockchain with a digital badge and loop count technology that enables the secured sharing of data among market participants, while improving the sorting, tracing and monitoring of plastics throughout the value chain. The result is a more competitive circular supply chain rather than a linear one, extending the lifecycle of plastics. Additionally, due to the increased transparency reciChain brings, the platform can provide better assurance to brand owners of the validity of the certificates they purchase from recyclers and converters.
Initially piloted by BASF in Brazil, the inspiration for reciChain came from a need in that market to deal with social inequality issues as well as regulatory concerns around the issuance of recycling certificates. Given its ability to tokenize the recycling value of plastics, the platform enables a fairer distribution of value added along the supply chain, even to cooperatives, which traditionally generate lower returns compared to other businesses. Moreover, the improved transparency from the material flow in the platform provides better compliance with recycling documentation. The project has already secured participation of some major Brazilian key players and will continue to be developed in parallel with the Canadian pilot.
"A successful implementation of reciChain will result in a collaborative digital consortium that will bring together plastic manufacturers, suppliers, government entities, retailers, waste collectors and recyclers aimed at keeping the life of plastic molecules circular," said Anthony DiPrinzio, Head of BASF Blockchain Lab. "Leveraging blockchain technology, we can work together to ensure our products deliver back to the value chain and contribute to a circular economy."
For the pilot project in British Columbia, BASF is working with Deloitte as a strategic advisor. The team is currently validating the pilot's value in the local supply chain with the goal of expanding it to a nation-wide solution in order to position Canada as a leading country in the recycling and recovery of plastics.
To learn more about reciChain and potential partnership opportunities, please visit www.basf.ca/reciChain.
Company info
2800 - 1055 Dunsmuir Street
4 Bentall Centre
Vancouver, BC
CA, V7X 1P4
Website:
deloitte.com/view/en_CA/ca/index.htm