How to start a corporate waste diversion program
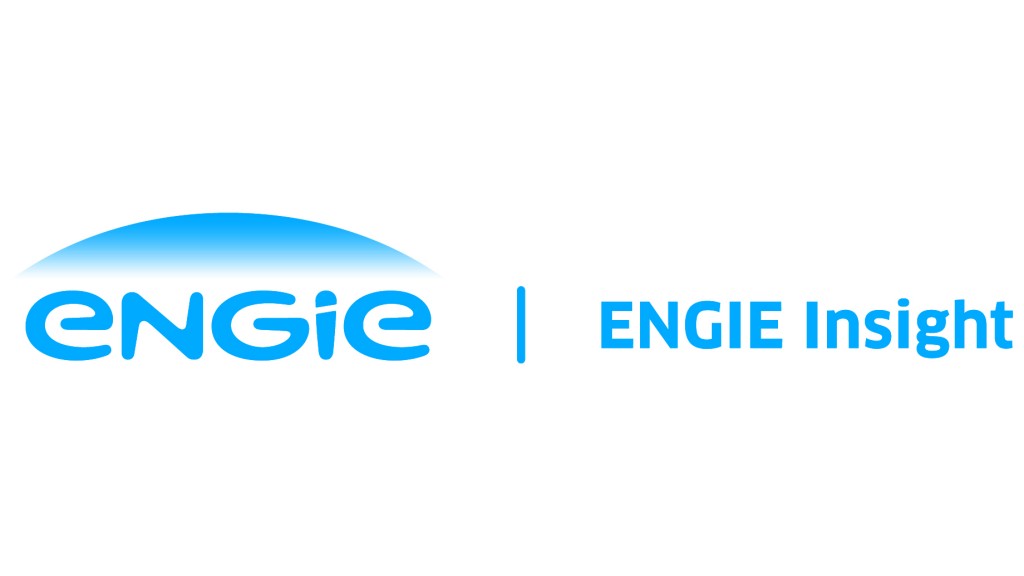
Today, corporations stand at the forefront of the sustainability movement. Amid worldwide recycling and waste management struggles driven by restrictive legislation, new programs and innovations continue to emerge that help businesses reduce their waste output. Investors want to see companies reporting on successful sustainability efforts. Incoming generations of consumers and the next wave of the workforce increasingly want to put their money and labor behind companies working to stem the threat of climate change. Strong business models now must include waste diversion programs, a corporate strategy that redirects waste from landfills.
Executing a corporate waste diversion program may appear daunting at the outset, but with the proper data collection, consistent implementation of best practices and employee buy-in, waste initiatives reduce operating costs for businesses and ultimately diminish their impact on the environment.
Gathering Data
Corporate waste programs need constant attention. With evolving waste regulations and programs, altering corporate expectations and equipment advances, these initiatives must be guided by a clear and well-run strategy.
Additionally, all departments and individuals, from the CEO to the frontlines, have to participate for the waste diversion program to succeed. But how do businesses even begin to put the necessary infrastructure in place? The first steps start with data collection and analysis.
Gathering data gives companies the base knowledge to understand where there is excessive waste, what should be cut back and how they should implement change. Quantitative and qualitative data both play a role in this process. Quantitative data helps businesses measure the return-on-investment (ROI) and what to focus on for waste diversion. This data includes waste composition by weight and percentage of waste per loading dock, providing insight into where waste is happening and what it's composed of. Qualitative data connects those findings to specific operational practices, helping businesses identify problem areas and solutions.
Businesses pull data from a variety of sources, including invoices and service contracts that provide service details and clarify where a company stands with its waste output, often inciting unexpected insights into its waste practices. Corporations commonly conduct waste audits to gain access to additional data that renders a more complete portrait of the areas of operation that create gratuitous waste and to spark new ideas to resolve the issues at hand.
Turning Data into Action
Once data collection is finished and a business has gleaned some insight into where corporations can cut waste, it's time to act. Companies can form the right strategy to make the appropriate employee habits stick. Commitment and consistency are necessary to make a corporate waste diversion program optimally effective.
Each company is unique - it has its own goals, processes, people and problem areas involved in the creation of waste. This means that each corporate waste diversion program will be unique as well, and should be treated as such. However, there are certain exercises that consistently encourage waste reduction and lower operating costs.
Embracing Good Habits
Best practices for corporate waste initiatives include:
1. Play into convenience - Encourage the right behaviors by making it as easy as possible for people to act on the desired sustainable behaviors. This may be implemented by matching waste disposal containers to the particular type of waste generated in a given space or ensuring that the containers are sized appropriately based on the waste stream.
2. Be conscious of signage and setup - Waste containers should be simple and easily identifiable. Color coding makes it easy for people to quickly and appropriately sort their waste, and mirroring city signage creates consistency that will encourage their participation. And don't be afraid of humor in signage - a witty message is more likely to engage someone in the process of waste disposal. The goal is to impact the behavior of your staff in a positive manner toward diversion and recycling.
3. Give incentive and opportunity - Motivate people to get involved by holding employee contests and urging them to take environmentally-friendly practices home with them. Given incentive and opportunity, employees are more likely to want to contribute.
4. Enforce habits - Ensure employees follow procedures in place for waste diversion programs. Programs like towel change opt-out in hotels or shutdown procedures of food and beverage machines in restaurants only work if employees are following through.
5. Engage Staff and Tenants - It's important that employees of all levels buy into their company's sustainability practices. Small-scale individual actions will add up to generate major cost savings for businesses. If one employee's buy-in encourages just three others, it can make a significant process towards the company's goals.
Waste Not, Want Not
Corporate waste diversion programs may initially appear intimidating to business leaders, however they're more simple than they seem if they start with solid data and consistent employee buy-in. While they do require attention, successful initiatives are mutually beneficial because they redirect waste away from landfills, realize millions in yearly savings, reduce emissions, comfort investors, and satisfy a new generation of the workforce and consumers.
It has never been more necessary to identify where businesses can cut excessive waste from their operational practices. Climate change is at the forefront of politics, science and education, and corporations are already a topic in the conversation around sustainability. By implementing waste diversion programs, they can begin to have a major voice in the conversation, too.
Arnold Bowers is Senior Director, Business Solutions at ENGIE Insight.