New sidewall protection for OTR tires designed for concrete and aggregates recycling
Innovative urethane protector dramatically reduces the risk of OTR tire sidewall punctures
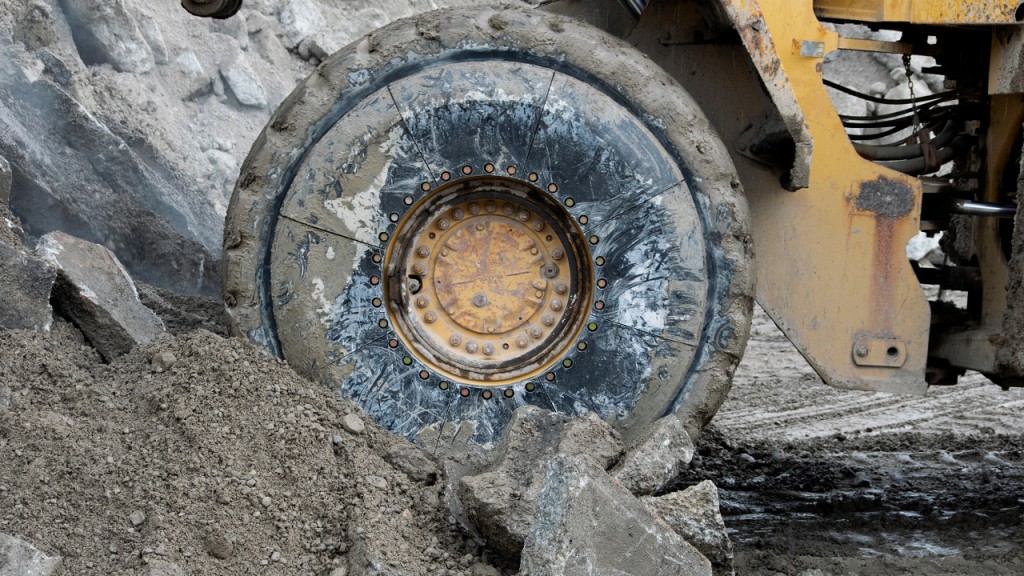
At concrete and aggregate recycling sites, recycled aggregate is produced by crushing concrete and asphalt to reuse the aggregate in the construction industry as a base for roads or building foundations. To keep operations running site managers rely on loaders to push large jagged chunks of torn up sidewalk, roadway or building materials - which can contain steel rebar - to the crushing line to reduce its size.
Even though OTR tires for heavy equipment are specially designed for harsh environments, the risk for damage is still high. One of the most common failure points is the tire's sidewall. Without added protection, the jagged edges and steel rebar in piles of debris can put loaders' OTR tires at severe risk of sidewall puncture and abrasion, particularly the front tires closest to myriad sharp, abrading objects.
Michigan-based firm, Argonics, which specializes in high-performance, polyurethane-based elastomers and which is one of the largest producers of impact, wear-resistant and customizable urethane products, has developed a new sidewall protection device for OTR tires. The company's sidewall protector is designed to stop loader sidewall punctures and abrasion while significantly extending tire life, to keep aggregate recycling operations reliably running, anduses a proprietary urethane formulation called Kryptane, which was engineered for extreme wear conditions involving abrasion, sliding or impact.
The solution is purpose-built for use on heavy equipment at aggregate recycling sites. Operators simply bolt on a polyurethane sidewall shield to prevent the sidewalls from getting punctured during operation.
Minimizing Costly Sidewall Puncture
Research by the Mechanical Engineering Department at the University of Alberta in 2011 on the detection of faults on off-road haul truck tires identified five tire failure areas: tire tread, shoulder, sidewall, bead, and liner. The study cited research by Syncrude Canada Ltd. that examined the causes for off-road tire failure from 2005-2010. Sidewall cuts accounted for approximately 18% of all faults, sidewall separation 10%, and sidewall impact over 5%.
When the sidewall is damaged in loaders, typically by a puncture, the vehicles are not safe to operate and the OTR tires are expensive to replace. Caterpillar 980 Wheel Loader OTR tires, for example, can cost up to $6,000 or more each. Repairing a damaged sidewall takes valuable time to send a tire out for repair, and the repair may not be successful. So, an aggregate recycling operator faces a sidelined loader, expensive tire replacement, and reduced production or even significant operational downtime.
With shortages for certain tire sizes more common recently, it could take days or longer to get a replacement tire installed at a repair facility, and then get the loader back to work. According to Argonics, the special properties of urethane make it an excellent material for sidewall protection. This tough, elastic material excels in preventing the penetration of sharp objects as well as deflecting them. It will change shape under impact and then return to its original shape afterward. Urethane also offers maximum abrasion resistance, which is ideal for situations where severe wear is a problem.
For these reasons, urethane is already being used at mining, heavy construction, and aggregate recycling sites across North America. According to Argonics, the idea for applying the special properties of urethane for off-road sidewall tire protection came from Perry Fell, Territory Manager at Luff Industries, a Canadian distributor of Argonics. He thought Argonics' expertise in high performance polyurethane elastomers would be well suited to an OTR application, and proposed the original design.
The sidewall protector comprises eight integrated segments that, together with a specially designed ring, use 32 bolts to apply to a wheel. The entire sidewall protector can be installed in about 15 minutes once the special flange has been installed by certified personnel.
The benefit of this design is that it allows easy replacement of just the segment of the protector that is damaged, if any, not the entire shield. Virtually no maintenance is needed other than to retorque the bolts after 15-20 hours of use - much like when installing new tires on a car.
The urethane-based sidewall protector has been tested at aggregate recycling sites in Toronto, Canada and Dallas, Texas. It has been installed on the front tires of Caterpillar 980 loaders at these sites.
"The sidewall protector has been performing very well," said Fell. "We've had no tire punctures or sidewall issues since installing the protectors."
Bob Welker, International Sales & Director of Marketing at Argonics, stated, "We've been able to refine the sidewall protector design based on the extended testing. There have really only been minor changes needed for things like increasing the size of the bolts." According to Welker, the patent-pending urethane sidewall protector is in its fourth generation. Currently the design is based on a 25" wheel diameter used by loaders such as the Caterpillar 980. The company is planning sidewall protectors for 33" and 45" wheel diameters next.
Minimizing Costly Sidewall Puncture
Research by the Mechanical Engineering Department at the University of Alberta in 2011 on the detection of faults on off-road haul truck tires identified five tire failure areas: tire tread, shoulder, sidewall, bead, and liner. The study cited research by Syncrude Canada Ltd. that examined the causes for off-road tire failure from 2005-2010. Sidewall cuts accounted for approximately 18% of all faults, sidewall separation 10%, and sidewall impact over 5%.
When the sidewall is damaged in loaders, typically by a puncture, the vehicles are not safe to operate and the OTR tires are expensive to replace. Caterpillar 980 Wheel Loader OTR tires, for example, can cost up to $6,000 or more each. Repairing a damaged sidewall takes valuable time to send a tire out for repair, and the repair may not be successful. So, an aggregate recycling operator faces a sidelined loader, expensive tire replacement, and reduced production or even significant operational downtime.
With shortages for certain tire sizes more common recently, it could take days or longer to get a replacement tire installed at a repair facility, and then get the loader back to work. According to Argonics, the special properties of urethane make it an excellent material for sidewall protection. This tough, elastic material excels in preventing the penetration of sharp objects as well as deflecting them. It will change shape under impact and then return to its original shape afterward. Urethane also offers maximum abrasion resistance, which is ideal for situations where severe wear is a problem.
For these reasons, urethane is already being used at mining, heavy construction, and aggregate recycling sites across North America. According to Argonics, the idea for applying the special properties of urethane for off-road sidewall tire protection came from Perry Fell, Territory Manager at Luff Industries, a Canadian distributor of Argonics. He thought Argonics' expertise in high performance polyurethane elastomers would be well suited to an OTR application, and proposed the original design.
The sidewall protector comprises eight integrated segments that, together with a specially designed ring, use 32 bolts to apply to a wheel. The entire sidewall protector can be installed in about 15 minutes once the special flange has been installed by certified personnel.
The benefit of this design is that it allows easy replacement of just the segment of the protector that is damaged, if any, not the entire shield. Virtually no maintenance is needed other than to retorque the bolts after 15-20 hours of use - much like when installing new tires on a car.
The urethane-based sidewall protector has been tested at aggregate recycling sites in Toronto, Canada and Dallas, Texas. It has been installed on the front tires of Caterpillar 980 loaders at these sites.
"The sidewall protector has been performing very well," said Fell. "We've had no tire punctures or sidewall issues since installing the protectors."
Bob Welker, International Sales & Director of Marketing at Argonics, stated, "We've been able to refine the sidewall protector design based on the extended testing. There have really only been minor changes needed for things like increasing the size of the bolts." According to Welker, the patent-pending urethane sidewall protector is in its fourth generation. Currently the design is based on a 25" wheel diameter used by loaders such as the Caterpillar 980. The company is planning sidewall protectors for 33" and 45" wheel diameters next.