L'OCCITANE and Loop Industries sign multi-year supply agreement to transition to 100 percent sustainable PET Plastic
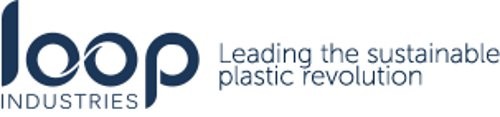
The L'OCCITANE Group, a global manufacturer and retailer of natural cosmetics and well-being products with five leading brands, and Loop Industries, Inc., a leading technology innovator in sustainable plastic, announced today the signing of a multi-year supply agreement for Loop branded 100 percent sustainable PET plastic. The agreement will see the L'OCCITANE en Provence brand start to incorporate Loop PET plastic into its product packaging as of 2022, enabling it to increase from its current 30 percent recycled plastic to reach 100 percent in its bottles by 2025 and place the Loop logo on all packaging containing Loop PET plastic.
As the demand for sustainable packaging solutions continues to grow, Loop Industries has emerged with transformational upcycling technology that allows plastic bottles and packaging, carpet and polyester textile of any colour, transparency or condition and even ocean plastics that have been degraded by the sun and salt, to provide brand owners a sustainable plastic product that helps solve the plastic pollution problem and meets FDA requirements for use in food-grade packaging. So, when the Loop logo appears on a package, it is a confirmation for consumers that the plastic is sustainable. It is a revolutionary development and L'OCCITANE is excited to be amongst the global brands partnering with Loop, as the group continues to innovate and set new industry standards.
"Helping companies leverage their packaging as a symbol of their commitment to sustainability rather than a symbol of waste is one of our primary missions. We are so pleased to work with the L'OCCITANE Group, a leading premium retail brand, to do just that," said Daniel Solomita, Founder & CEO of Loop Industries. "We are convinced that companies that make this transition, use sustainable packaging and encourage recycling, will help restore our environment and create greater economic value."
The L'OCCITANE Group has always been very conscious of the impact of packaging and the fundamental importance of eco-design and recycling. With nature at the heart of its business, the group is committed to limiting its impact on the environment at every possible step, from product formulation and sustainable packaging through to final product distribution. The company first introduced eco-refills in 2008 and currently proposes 15 L'OCCITANE en Provence eco-refill products. These not only use up to 90% less packaging than the original containers (representing a saving of 121 tons in 2018), but also lower CO2 emissions thanks to the reduced product transport. The group is working with specialised suppliers to design lighter packaging that prioritises recycled materials, and aims to increase its current 84% technically recyclable plastic to 100% by 2025.
Both Loop and L'OCCITANE know how important it is to keep plastic in the economy and out of our shared environment. This agreement supercharges L'OCCITANE's ability to close the loop on its plastic bottles. L'OCCITANE is going even further and is providing in-store recycling facilities to encourage its customers to participate as well. Since 2014, L'OCCITANE has been working with TerraCycle® to provide in-store recycling facilities for empty cosmetics containers and now offers in-store recycling at 30% of its owned stores across the world, aiming to reach 100% by 2025.
For Adrien Geiger, Global Brand Director at L'OCCITANE en Provence: "Our brand is inspired by nature, people and culture and we have been using natural plant-derived ingredients and eco-friendly manufacturing for more than 40 years. We are therefore very conscious of the importance of eco-design and sustainable packaging. We have been launching eco-refill products, in-store recycling and bottles made out of 100% recycled plastic for more than 10 years and are continuing to progress on this. The innovative technology that Loop provides is a game-changer that can help us fundamentally contribute to solving the growing global concern about plastic pollution. We are excited to sign with Loop, representing a significant shift in our approach to plastic."
The L'OCCITANE Group is using the Sustainable Development Goals as a framework to proactively address its environmental challenges and contribute towards the global effort to reduce plastic pollution. As part of this, L'OCCITANE en Provence has signed the Ellen MacArthur Foundation's New Plastics Economy Global Commitment, an initiative that is driving action with businesses and governments to work on solutions that address the root and causes of plastic waste and pollution.
Loop Industries, Inc. is a technology company whose mission is to accelerate the world's shift toward sustainable plastic and away from our dependence on fossil fuels. Loop's patented and proprietary technology decouples plastic from fossil fuels by depolymerizing waste polyester plastic and fiber to its base building blocks (monomers). The monomers are then filtered, purified and repolymerized to create virgin-quality polyester plastic suitable for use in in food-grade packaging.