New conveyor feed boosts yield of Eddy Current Separator
Product distributor replaces vibratory chute and prevents clogging
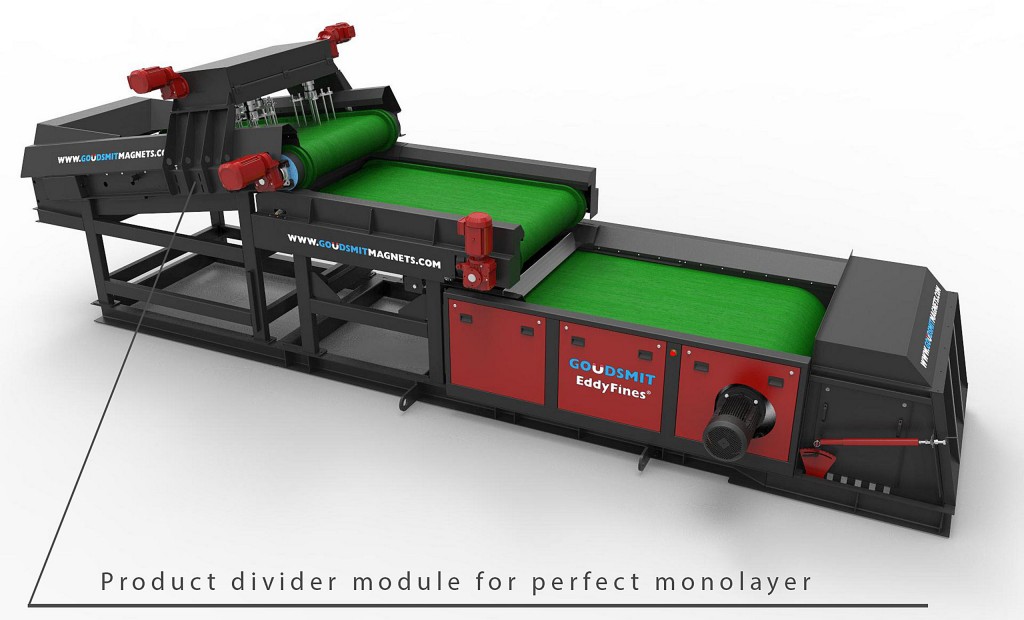
The conveyor feed recently developed by Goudsmit Magnetics consists of a conveyor belt feed that is supplied by a product distributor. This prevents clogging of the vibratory chute during the recycling process and increases the yield of non-ferrous metals. Sticky or damp product streams, such as incinerator bottom ash (IBA) and refuse-derived fuel (RDF) adhere to the surface of vibratory chutes, preventing them from distributing the product evenly. The product takes on a preferred orientation (the path of least resistance) preventing formation of a homogeneous layer, which results in reduced yield of non-ferrous metals.
Until now, a common solution to this problem was to clean the feed belt or vibratory chute at weekly or monthly intervals. This, however, means unnecessary downtime and extra maintenance. The true cause of the problem is the encrusted vibratory feeder. This newly developed conveyor feed with product distributor prevents this problem by creating a mono-layer that ensures full belt coverage. This means maximum utilization of the capacity and separation efficiency of the magnetic separator, as well as longer service life of the conveyor.
Mono-layer
A mono-layer is a product layer that has a maximum thickness of one piece; in other words, there are no pieces lying on top of each other. This is important for eddy current separation, because the non-ferrous pieces in the product flow are 'ejected'. If there were sand or a stone on a piece of metal, for example, there is a good chance that the EC separator would not eject the metal particle far enough to separate it from the product flow. Particularly for the 'fine fractions' (particle size: 0-10 mm) it is extremely important to create a mono-layer for maximum recovery of non-ferrous material. The system actually consists of three conveyor belts, each with its own task.
Three conveyor belts
The first conveyor belt is at an angle and feeds the material until it reaches the product distributors or 'churners'. These turn through the material and distribute it evenly so it lies on the belt as a single mono-layer and completely covers it. This is an excellent solution for damp or sticky product flows with 0 - 50 mm fractions, such as incinerator bottom ash (IBA), refuse-derived fuel (RDF) and automotive shredder residue (ASR). If the amount of material being fed in exceeds the capacity, the excess material slides back down. This ensures a constant volume and continuous flow to the next processing step.
The second conveyor belt (magnetic separator) is flat and transports the material towards the end of the belt and the magnetic head roller. Here ferrous parts are deflected and separated. The third conveyor (eddy current separator) is now supplied with an optimum material flow: a mono-layer, perfectly spread across the entire width of the belt and free from fluctuations in density. The ferrous metals are also removed so they do not interfere with the eddy current separation step.
The material is now perfectly prepared and ready for the powerful 38HI eddy current rotor, with a gauss value of 3500 at the belt (2.4 mm thick). This high magnetic force is necessary for heavy pieces of non-ferrous metal, such as copper and brass. The end result of the complete machine: optimum ferrous and non-ferrous separation without time-consuming machine downtime for cleaning encrusted vibratory chutes.
Eddy current separators
Eddy-current or non-ferrous separators consist of a conveyor belt system with a rapidly rotating magnetic rotor at the end. The rotation speed of the magnets generates an induction field, creating a rapidly changing magnetic field (see video). The separation is based on the principle that every electrically conductive particle that is located in an alternating magnetic field becomes temporarily magnetized itself. Simply put: For a brief moment all the non-ferrous metals that pass the magnetic roller become magnetized themselves, causing them to be 'ejected'. This makes it possible to separate a great many non-ferrous metals and alloys, including aluminium, copper and brass.