Lead batteries: the sustainable back-up power resource for the future
Lead batteries still serve as our most sustainable back-up power source
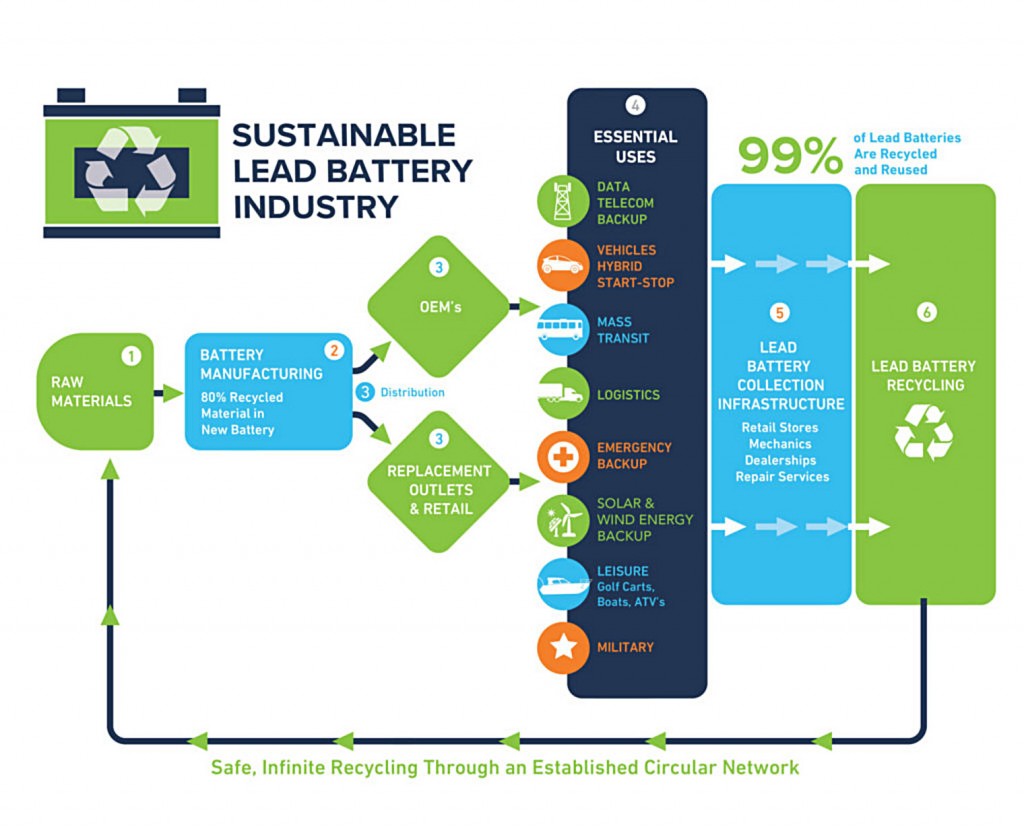
History tells us the lead battery as we now know it was invented 1859 by French physicist Gaston Planté. As the oldest rechargeable power source, one of the first applications of Plante's lead acid battery powered the lights in train cars while stopped at a station.
Since then other batteries and battery chemistries have come and gone and newer chemistries are advancing to get to the same level of sustainability as lead batteries. But today, lead batteries still serve as the most sustainable back-up power source we use. You'll find them in cars, boats, power stations, data centers, cell phone towers, children's toys, emergency lighting and a myriad of other uses.
Lead batteries are sustainable because they are recyclable. In fact, the vast majority of new lead batteries are made with raw material from scrap lead batteries. According the Battery Council International (BCI), 99 percent of all lead batteries manufactured are recycled. In 2017, Interstate Batteries alone recycled more than 1 billion pounds of lead batteries which will be used to make new batteries.
In an on-line brochure entitled "The Facts About Lead, the Energy Solution" produced by the BCI, "Innovative recycling facilities have been developed to recycle virtually 100 percent of a lead-acid battery's components. Collection, transportation, and handling of spent lead-acid batteries are well defined and regulated by the US government and by most states." The same thing cannot be said about lithium batteries.
Comparing lead to Lithium
The LA Times published an article in March 2018 explaining that less than 3 percent of lithium-ion batteries around the world are recycled according to Zheng Chen, a 31-year-old nanoengineer at the Sustainable Power and Energy Center at UC San Diego's Jacobs School of Engineering. Other industry articles suggest maybe up to 5 percent of lithium batteries being manufactured are recycled. Since only a small percentage of lithium and lithium batteries are being recycled, the batteries from used smartphones and laptops tossed in household garbage end up in trash trucks and landfills where if damaged, can create thermal runaways and fires.
Researchers are also questioning the longevity of lithium supplies as well as the sustainability of other minerals and metals needed to allow a lithium battery to work. Cathode materials such as cobalt are a concern.
Most of the world's Cobalt is mined out of the Democratic Republic of the Congo in Central Africa (DRC). In an 87-page report published by Amnesty International and African Resources Watch (Afrewatch) in 2016, they discovered children as young as 7 years old were working in cobalt mines. It is no secret that children mine cobalt in the DRC. The US Department of Labor has listed it as a "good produced by child labor since at least 2009."
However, since cobalt prices have skyrocketed in the last few years, battery manufactures are seeking to find less expensive materials to use with the lithium to make batteries. And lithium batteries have not yet developed the same kind of recycling infrastructure that the reliable, long-serving lead batteries have.
Presentations at the annual Battery Show in Novi, Michigan, Sept. 10-12 emphasized that makers of lead batteries continue to refine the performance and design of their products. Lead batteries will continue to be an important part of newer, electronic vehicle operating systems. They will still be used to start the vehicle and they allow for regenerative braking, the process that gives these vehicles the ability to save their own energy to power the vehicle when idling or driving at low speeds.
A closed-loop process with a future
The recycling process for lead batteries remains circular, or in a closed loop, therefore diverting virtually all lead batteries away from land-fills and improper disposal. The battery case is made of polypropylene; the plates are made of lead; water and acid is mixed to make electrolyte and it can all be recycled. The battery casing and plates are easily melted down and reformed and the electrolyte can be neutralized and reused. One use for the electrolyte is to convert it to sodium sulfate, an odorless white powder that's used in laundry detergent, glass and textile manufacturing.
As for the continued rhetoric about emissions related to lead battery recycling, an article published Aug. 14 by TBS Engineering Group, a world leader in battery automation, explains what the lead battery industry is doing to improve the environment.
"By 2020, it is predicted that start-stop technology utilizing lead batteries will help eliminate 2 million tons of vehicle greenhouse gas emissions annually in the U.S. alone. This is equivalent to the annual energy use of 211,000 average U.S. households."
The ever-growing number of electric and hybrid vehicles being manufactured use an SLI (Starting, Lighting, Ignition) battery to start the car. "By 2035 there will be over 2 billion cars on the world's roads - the majority of which will include a lead battery," according to TBS Engineering.
Company info
12770 Merit Drive, Suite 1000
Dallas, TX
US, 75251
Website:
interstatebatteries.com/recycling
Phone number:
972-715-6694