Making the case for retreads in waste and recycling
The right casing, modern techniques and proactive maintenance can provide additional life and value for used tires
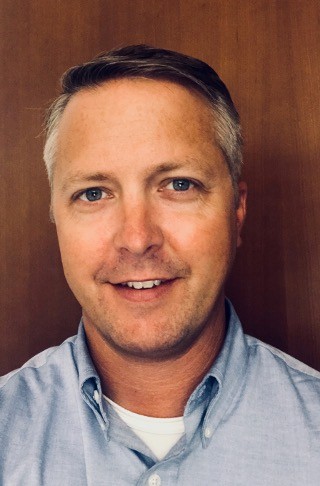
Refuse and recycling collection fleets are challenged every day by some of the most severe hauling environments. From residential locations to inner city streets to landfills, waste fleets must tackle challenging routes to get the job done. These harsh operating conditions can cause tires to wear more quickly which leads to frequent need for replacement; this has significant cost implications for fleets.
This is where retreads come in. Retreading is a waste fleet best practice that maximizes tire casing life and helps ensure fleets get the most out of their tire investment.
Common misconceptions about the safety and reliability of retreads discourage some fleets from incorporating them into their tire program. However, the commercial truck tire industry is advancing rapidly, backed by sophisticated technologies. Retreads are no exception. The retreading process has progressed significantly over the last few years in particular with the integration of advanced technology into both the inspection and product development processes. Today, retread manufacturers work closely with dealers and retreaders to ensure the highest standards of quality are maintained throughout the retreading process, from buying tread rubber to getting retreads to market.
Casing matters
An efficient retread program starts with the right casing. Every tire casing is designed with specific performance attributes based on the application needs. Fleets need to start with a quality casing engineered with higher retreadability - one that is durable in high-scrub and short-haul environments and touts longer wear performance. Premium casings are engineered to work with quality retreads to capitalize on the unused potential of the casings once removed.
Fleets which retread are simply ahead of the game. On average, refuse fleets can retread tire casings every three to six months and between two and three times per casing, which taps into extra mileage potential.
The modern retreading process
Retreading is a multi-step process that begins with a careful casing inspection, performed by highly trained specialists using sophisticated technology like shearography to check for anomalies unseen by the naked eye. Shearography is an advanced system to uncover separations in the belt package, liner and bead areas of a casing. The process, which is designed to ensure product quality and safety, takes 240 videos, detects air movement smaller than the width of a human hair and completes a bead-to-bead scan in less than two minutes.
Any casing inconsistencies detected during initial inspection are repaired before a new tread is applied. After repair, the casing is retreaded through a multi-step process, which includes buffing (removal of any remaining tread) and curing of a new tread on the tire casing. Once complete, the casing is again inspected a final time before being returned to service. This proven process is robust and designed to ensure high-quality retreaded tires.
Proactive maintenance and monitoring
A proper tire maintenance program is key to ensure reliable performance on the road and help prevent premature removal of tires and downtime. Refuse fleets that are proactive in their tire care best practices - consistently conducting pre- and post-trip inspections and regular yard checks, and routinely rotating tires and inspecting casings for road-related or operationally related damage - typically do a better job of caring for casings to ensure they can be retreaded in the future.
Tracking performance is also critical to ensuring fleets get the most out of a tire and retread program. Fleets should look to partner with dealers that have capability to monitor and record retread performance, repair history, inventory and casing rejection information in real time. For example, Bandag's tire management system, BASys, provides actionable insights to refuse fleets so they can make informed decisions about their tires.
Knowing the integrity of casings and how many times they have been retreaded helps ensure assets are being used to their full potential and performance.
A trusted dealer network should be considered crucial in designing and maintaining a custom tire program tailored to meet the needs of a waste collection fleet. By understanding the business needs of a fleet, a dealer can ensure that the right tire is selected for the job and that a fleet's tire assets are well-maintained for long life and can be retreaded when needed.
The bottom line
There's no doubt waste fleets have a unique set of tire needs to operate efficiently and profitably. Retreads can help fleets make mobility more efficient by capitalizing on tire performance potential, and by integrating technology into the retread process and proactive maintenance practices, waste and recycling fleets can be assured that retreads provide a reliable and profitable solution to get the job done.
This article was provided by Bridgestone Americas. Ryan Hannah, as product manager, commercial group at Bridgestone Americas Tire Operations, leads new product development and strategic product category planning.
This article was originally published in Recycling Product News, July/August 2018, Volume 26, N. 5.