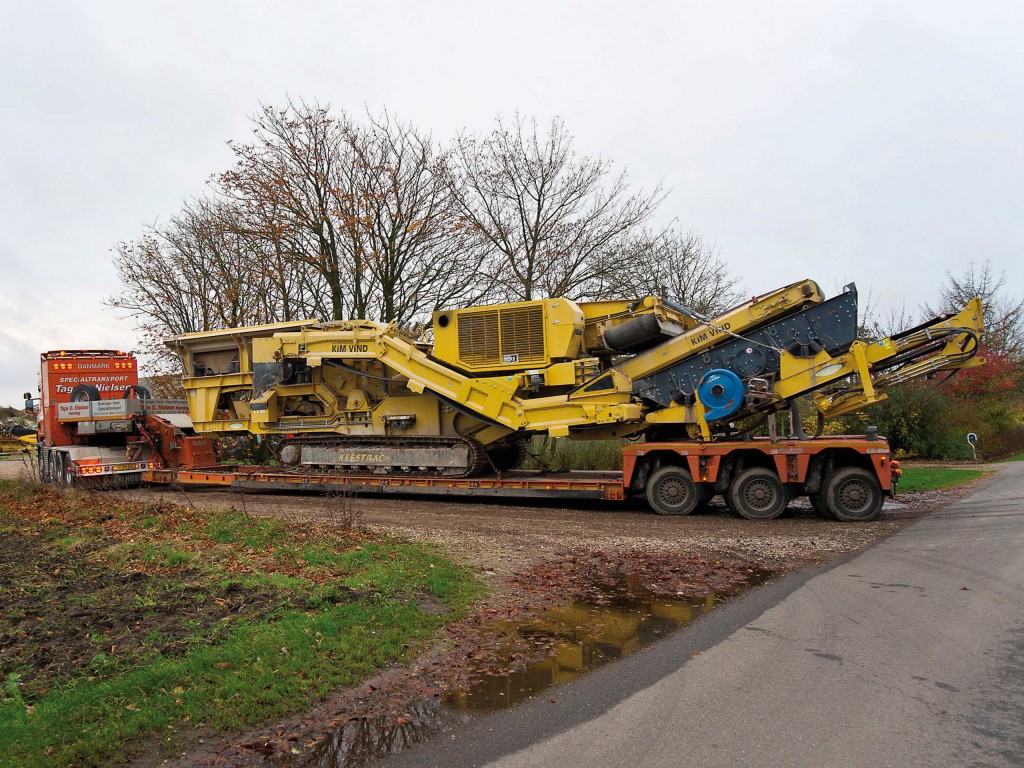
At CONEXPO 2017 KEESTRACK displayed the tracked impactor R3, the smallest unit of its impactor range and the 55-ton R5.
- What is the intended application, material type and amount of material to be processed, as well as end-product desired, and what are the projected costs per ton, after purchase, for running the machine?
- What are the environmental considerations applicable in the area where the machine will operate, and is electric power readily available and cost-effective?
- What are the key technical specifications of the model being considered, including: engine horsepower, weight of rotor and blow bars, as well as hopper capacity, feeding height, machine weight, dimensions and ease of transport?
- Is the rotor drive direct-drive from the engine, electric-drive or hydraulic-drive?
- Does the model being considered have the capability to track (move) while crushing?
- Will your impact crusher be used in tandem with a jaw crusher or a screen plant, and how will product flow through your system?
- Would a built-in screen be beneficial, and what other options, including magnetic separation, conveying, feeders and integrated systems need to be considered?
- What type/quality are key components, including wear parts, hydraulics and electronics, and what is the type and quality of steel used in frame, crusher housing and rotor?
- Does the impact crusher have a user friendly design, with ease of changing blow bars, and ease of access for maintenance and servicing?
- If a part is needed, what is the turn-around time from your distributor or manufacturer?
This top-ten list is excerpted from the RPN article, "The Rise of Mobile Impact Crushers for Recycling", from the March 2017 edition, Volume 25, Number 2.