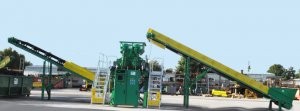
Columbus McKinnon Corporation (CM) has developed their new CM Hybrid Primary Shredder to adapt to the ever-changing markets in the tire recycling industry as well as expand into new markets beyond tires.
Since entering into the business in 1982, CM says all their tire shredders have exclusively used Holman Patent Technology or Fixed Rotor Technology for the reduction of tires. This technology creates very close knife-to-knife tolerances that are within 0.001 - 0.002 of an inch, which allows the machine to produce cleanly cut tire chips.
The superior quality produced from this type of cut has always been preferred when making TDA or TDF product. However, with the growth of the Crumb Rubber Industry shredder requirements are evolving. Shredders within these applications are used for volume reduction to prepare the tire for additional processing, allowing for other cutting technologies to be considered.
The CM Hybrid Shredder is a primary unit that was developed for multiple uses within the tire industry as well as other applications. By using Removable Rotor Technology the machine becomes a “Hybrid” system. The machine can use Holman Patent Technology that has been adapted to a Removable Rotor, which works well for tire applications as well as other applications where close cutting tolerances are required. It also accepts single piece shear shredder knives that are common for shredding in general waste applications. CM says this combination allows the machine to be particularly versatile within the waste and recycling industry.
CM engineers have also developed new knife group locking technology and advanced bearing protection to enhance the machines performance. The “CM Secure Lock” system allows the bearings to be located outside of the shredding enve- lope for better protection and is no longer used to secure the knife group.
Key features of CM's new hybrid shredder include fast and easy maintenance in the field; Stack and Go Hardened Rotors that provide less downtime for fast and simple knife changes; removable end plates for blade holder and spacer replacement; interchangeable cutting options; and CM hexagon shafts made from hardened steel allow for easy rotor and knife changes in the field.
Plus, standard CM knives can now be bolted directly to the rotor without wear plates or tie bars. Units utilize standard CM patented knives or new CM Shear Blades, and users can create a multitude of cutting configurations by swapping out different size knives and shear blades to create larger or smaller cuts.
Other standard features include: twin 75-hp motors; large 63”l. x 58”w. cutting chamber; chamber plates on each end of shaft to protect bearings and seals; auto reverse; a PLC touch screen; Advanced safety features throughout the system; and a Soft Start package.