Combination PET and HDPE washing plant built in UK
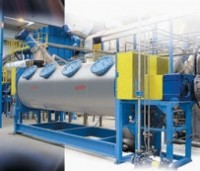
At the Plastic Recycling Conference held this past February in Florida, AMUT announced that its new dual line washing plant is fully operational, and capable of producing 2,000 kilograms per hour of high quality clean R-PET, and 2,000 kilograms per hour of high quality clean R-HDPE. Purchased by Intercontinental Recycling in England, the plant has been running since early this year – both lines producing for “bottle to bottle” applications.
The plant is constructed with a front end sorting plant which separates the co-mingled post-consumer stream to its respective plastic washing and processing operations, while baling the metals and paper streams for resale. The PET washing plant produces flake used for bottle to bottle applications, and the washing process uses the AMUT patented washing technology and a patented AX-Friction Washer Machine (shown left). The PE washing plant is complemented with the same patented washing technology and has an AMUT EA 180 single screw extruder, which pelletizes the clean PE flakes. The flakes are extremely clean, so that the screen changer only indexes once every few hours, for pelletizing dirty post-consumer material. Both washing lines utilize AMUT closed loop water filtration and heat exchanger technologies for high levels of cost effectiveness and environmentally friendly operation. Further reduction in operational costs is seen by the lack of manual labour, due to the line’s automation.
AMUT also recently completed the construction and startup of the world’s first totally closed-loop AMUT ‘TWIN’ plant technology. “This plant consists of two complete washing lines, one for PET bottles and the other for PE milk bottles,” explains Anthony S. Georges, president, AMUT North America, Inc. “The line is fed automatically from the post-consumer waste stream, sorted for PET bottles and milk bottles, where they go to each of their own individual washing plants that produce 2,000 kilograms per hour of high quality bottle-grade material.”
The plant is constructed with a front end sorting plant which separates the co-mingled post-consumer stream to its respective plastic washing and processing operations, while baling the metals and paper streams for resale. The PET washing plant produces flake used for bottle to bottle applications, and the washing process uses the AMUT patented washing technology and a patented AX-Friction Washer Machine (shown left). The PE washing plant is complemented with the same patented washing technology and has an AMUT EA 180 single screw extruder, which pelletizes the clean PE flakes. The flakes are extremely clean, so that the screen changer only indexes once every few hours, for pelletizing dirty post-consumer material. Both washing lines utilize AMUT closed loop water filtration and heat exchanger technologies for high levels of cost effectiveness and environmentally friendly operation. Further reduction in operational costs is seen by the lack of manual labour, due to the line’s automation.
AMUT also recently completed the construction and startup of the world’s first totally closed-loop AMUT ‘TWIN’ plant technology. “This plant consists of two complete washing lines, one for PET bottles and the other for PE milk bottles,” explains Anthony S. Georges, president, AMUT North America, Inc. “The line is fed automatically from the post-consumer waste stream, sorted for PET bottles and milk bottles, where they go to each of their own individual washing plants that produce 2,000 kilograms per hour of high quality bottle-grade material.”