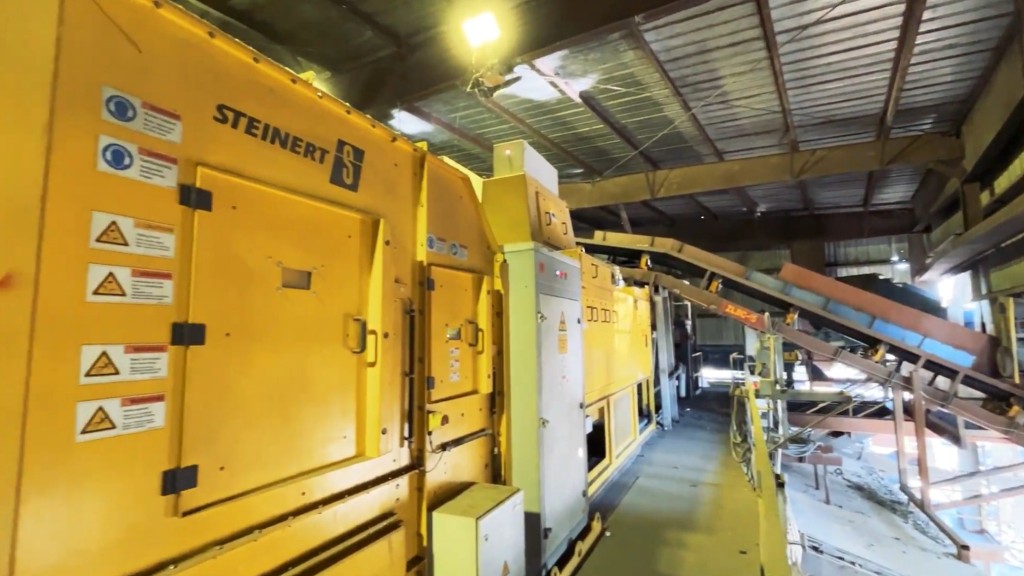
George Adams, CEO of SA Recycling, has shared insights into the company's growth, sustainability efforts, and the significant role of STEINERT technology in their operations. Omar Bravo, general manager of the Anaheim plant in California, highlights the ground-level innovations driving the company's success.
"I began driving tow trucks when I was 17," said Adams. "Later I started working alongside my father for 40 something years. My two brothers also work in the company and are my partners and after all these years we're still really close. Then, my sons came into the business after they finished college. So, I guess that's what makes it the most fun. It's working with my sons."
Ultimately, however, it is George Adams' leadership, which has been fundamental in steering SA Recycling to success. Adams' participation in global recycling organizations such as ISRI and BIR highlight the company's dedication to recycling and navigating global political terrain to help achieve worldwide sustainability.
SA Recycling's journey started in Anaheim, California, where today 250,000 metric tonnes of shredded materials are processed a year. Adams recalls the evolution and expansion of the company's facilities, highlighting Anaheim as a hub for research and development for SA.
Reliable sorting systems for processing light and heavy metals
In terms of recycling capabilities, Adams praised the company's relationship with STEINERT.
"We have utilised their eddy current separators for quite some time now in many of our locations to get most of our non-ferrous metals. For approximately four years, we have also been using their multi-sensor sorters, primarily to upgrade Zorba to Twitch, meaning to extract an aluminum mix from a non-ferrous metal stream."
The STEINERT KSS | XT CLI combines four sensors. Two optical sensors offer colour and three-dimensional shape data, while the inductive sensor identifies metals. Density variances are recognized using X-ray transmission (XRT). In the meantime, Omar Bravo points out the outstanding flexibility and accuracy: "Depending on which product our customer requires, we select the right program and sort up to 99 percent pure aluminium or eliminate magnesium from the product stream at the touch of a button."
X-ray fluorescence technology (XRF) is also in use in Anaheim. Since 2019, STEINERT CHUTEC XRF-sorter efficiently segregates heavy metals into metal types such as copper, brass, zinc, or stainless steel, which opens up new sales potential for SA Recycling.
While Omar Bravo appreciates the longevity of the X-ray sorters, of which he still hasn't had to replace a single sensor in four years, George Adams is particularly enthusiastic about the eddy current separators.
"When we started measuring, the big thing was that they had a faster belt speed on their machine than what other people had," said Adams. "The even bigger thing is that over the years we have realised, that we simply don't lose bearings on their eddy currents – they just don't break, ever".
Accurate metal separation
George Adams emphasizes a comprehensive recycling ecosystem that extends beyond metal. While he acknowledges solar power as a positive step, Adams focuses on maximizing metal recycling to reduce the greenhouse gases generated in the production of primary metals.
Adams sees STEINERT's advancements in LIBS technology for aluminum alloy sorting as the direction the industry is heading - with an emphasis on precision separation to meet the demand for specialty alloys that are being returned to the U.S.
"I think the harder thing right now is adapting to the next phase, which is using equipment to get specific segregated alloys. Because I think that's really going to be the future of metal recycling. Everybody wants segregated alloys," said Adams.