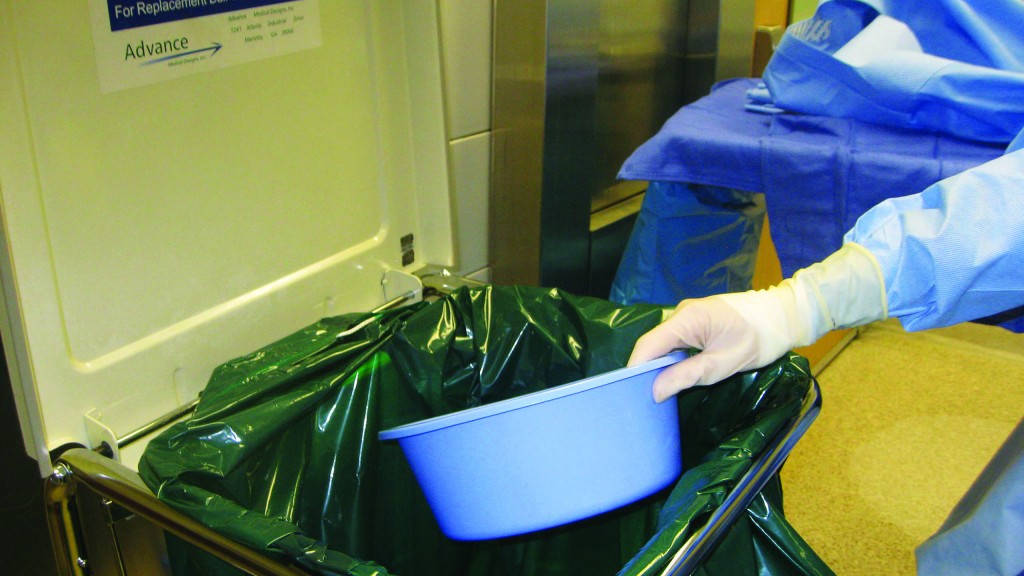
On a global basis only about 14 percent of plastic packaging is collected for recycling, and across the healthcare sector these rates are significantly lower. As noted in the World Economic Forum's 2016 white paper, The New Plastics Economy: Rethinking the Future of Plastics: "Today's plastics economy is highly fragmented. The lack of standards and coordination across the value chain has allowed a proliferation of materials, formats, labelling, collection schemes, and sorting and reprocessing systems, which collectively hamper the development of effective markets. The development and introduction of new packaging materials and formats across global supply and distribution chains is happening far faster and is largely disconnected from the development and deployment of corresponding after-use systems and infrastructure."
With the exception of durable goods and the currently limited amount of recycling of plastic products and packaging from clinical settings, plastics used in the healthcare industry are typically single use materials representing a linear "take-make-dispose" economy.
Considering all of this, the Healthcare Plastics Recycling Council (HPRC) and Plastics Industry Association (PLASTICS) are asking the question: Is it possible to radically increase the amount of clinical healthcare plastics managed and recycled by implementing a circular "make-use-return" economy?
THE POTENTIAL SOLUTION
To answer this question, HPRC and PLASTICS designed and implemented a multi-hospital plastics recycling project in the Chicago market. Focused on non-infectious plastic packaging and products collected from clinical areas of the hospitals, the project sought to demonstrate a viable business model for the recycling of healthcare plastics on a regional basis.
Prior HPRC-sponsored efforts included pilot projects at individual hospitals, but one of the barriers preventing these projects from achieving economic viability was that the quantity of materials generated by a single hospital did not represent sufficient commodity value necessary to attract the attention of recyclers.
In bringing together multiple hospitals in the same geographic area, the Chicago regional project hoped to overcome this barrier. The project's aim: to demonstrate that these plastic materials have value, that they can be effectively collected from hospital clinical areas, and that they can be collected in sufficient quantities to surpass the economic tipping point, such that recycling of these materials represents a good business opportunity for recyclers.
Participating hospitals collected a variety of healthcare plastics (primarily from main operating rooms and ambulatory surgery centres) including products and packaging made of polypropylene, polyethylene and other resins in the form of sterilization wrap, irrigation bottles, basins, pitchers, trays, Tyvek, and rigid and flexible packaging materials.
These materials were then transported by waste haulers to material recovery facilities (MRFs) for processing or transferred to specialized plastics recyclers. It is at the MRFs that the project team performed assessments to determine material composition and quality.
THE PROCESS
Following the engagement of stakeholders, the project team worked with recyclers and waste haulers to define which materials were acceptable based on the capabilities and acceptance criteria of the MRF or recycler processing the materials. Internal champions were identified within the hospitals, and for hospitals which did not have existing clinical area recycling programs, staff training sessions were planned and implemented.
Materials were collected in single-stream, commingled fashion using colour-coded bags, and were conveyed to the recycler using existing handling systems that are already in place for collection, accumulation and transportation of cardboard, ledger paper, cans and bottles. Assuming a single stream recycling program is already in place at the hospital (as was the case with all project participants) and supported by the hospital's waste hauler, clinical materials may be transferred within the hospital, accumulated and transported to the waste hauler's MRF using equipment, labour, and processes that are already in place, thereby avoiding separate handling costs and transportation charges. This also eliminates the environmental impacts of having separate pickup of materials at the hospitals.
However, the downside of utilizing the waste hauler's single-stream pathway include an increased chance of contamination from other recyclables in the shipping container (typically a compactor), increased likelihood that the bags of recyclables rupture in the compaction process, and implied additional handling of bags which must be separated from other recyclables at the MRF or recycling facility for accumulation and transfer to the plastics recycler (unless the MRF is capable of sorting and processing the healthcare plastics).
Alternatives to single-stream recycling included using a reverse distribution model where materials are accumulated and transported from the hospital by a service provider who already has transportation equipment making deliveries or other pickups at the facility. Some examples included firms delivering medical supplies and equipment as well as document destruction companies.
The primary benefit of using a reverse distribution pathway for plastics accumulation and transportation is that materials are handled separately from solid waste and other recyclables, thereby reducing the potential for contamination from these materials.
The project saw success around the collection of sterilization wrap, a non-woven product manufactured from polypropylene resin, which represented the highest volume of material collected, and comprised up to 47 percent of the shipments by weight, depending on the recycler's acceptance criteria. As part of this project, the material properties of sterilization wrap were evaluated as a viable substitute or supplement for virgin resins in product manufacturing. Other flexible packaging materials such as film plastics, as well as rigid plastic packaging, were also collected in considerable and consistent quantities.
COLLECTING INSIGHTS
Some of the "big-picture" takeaways from this pilot project include the following:
Keep it Simple: Collection of clinical plastics must be simple for participating clinical staff in order to be effective. Including several types of plastics in the program while excluding others placed a significant burden on clinicians to sort materials at the source, given their primary focus of ensuring positive patient outcomes. In addition to a simple collection process, there must be clear handling methods for accumulated materials. Once recovered, the packaged materials must be clearly distinguishable from other types of waste and recyclables, and handling practices of accumulated materials must be simplified as much as possible to ensure that materials are delivered to proper containers or processing areas.
Find Your Champions: Critical to program success is the engagement and commitment of program champions within each stakeholder group who can assist with training, audits, and reinforcing the behaviours necessary to ensure effective material collection. All stakeholders must see tangible benefits from participation, and those benefits must outweigh the costs of both starting and maintaining the program. It is vital to be fully committed and have champions at each level. Having this support in place at the participating hospitals, as well as the haulers and recyclers, made a significant impact on the project's success. Not having that support in place would have been disastrous.
Commingled Materials have Marginal Value: Ideally, a hospital will create a partnership with a recycler/processor that is flexible and willing to modify current practices to access a new source of recyclable materials. All parties need to recognize that once commingled, clinical plastics have limited value, and extracting value from individual components requires detailed sorting. However, determining who will be responsible for this sorting can be a challenge.
Most hospitals and healthcare networks are unwilling or unable to take on this responsibility - this creates the need to identify a partner capable of mechanical sorting, to consider creative alternatives such as partnerships with organizations and industry, or to focus efforts on a single type of material and consider additional materials after systems are established.
Keep an Eye on the Economics: To attract the attention of recyclers and their customers, hospitals must accumulate materials in sufficient volume, and processes must be in place to ensure a clean, continuous supply. This is necessary for securing the end users' commitment to incorporate the recycled materials into their products, thereby providing a demand for the materials necessary to keep the program running. A recycling program's economic viability is a function of market pricing, so stakeholders must think through the economic "tipping point" and consider market volatility when evaluating the financial costs of collecting, aggregating, transporting, processing and marketing materials from a clinical source. Ultimately the economics of a project must be favourable to recyclers if the program is to be sustainable. Including certain types of materials in the program may not be possible based on recycled commodity value.
TAKING ACTION
This project, while just a first step into exploring the possibilities of regional collaboration, has yielded a number of practical actions that both hospitals and recyclers can take to facilitate increased healthcare plastics recycling.
Hospitals
• Start simple, with one high-value material, and build on its success once the program is established.
• Explore recyclable material transportation options outside of traditional solid waste hauling and recycling contracts.
• Continue to reinforce staff education to prevent contamination and maintain the quality of your stream.
Recyclers
• Approach a hospital system or multiple hospitals in a region so you can reach adequate volumes to sustain the program.
• Work with hospitals to mitigate contamination risk in the collection process, such as having bags tied off and removed before the patient enters the room.
The Chicago regional cooperation project has confirmed that certain types of plastics commonly found in clinical settings can be profitably recycled, including sterilization wrap (PP, #5), saline bottles (PP, #5), polyethylene terephthalate glycol-modified packaging trays (PETG, #1), and possibly other types of flexible and rigid materials.
In addition to exploring mechanical recycling opportunities for these various plastic materials, the team also tested the potential to demonstrate value through energy conversion and chemical recycling.
The project team partnered with RES Polyflow, an Ohio-based company that makes energy products from difficult to recycle polymer and rubber waste, to process a sample of healthcare plastics in their pyrolysis system, which converts plastics into liquid fuel products. The team also sent PETG packaging trays to another company that specializes in chemical recycling, where the PETG was converted to polyols for use in foams, coatings and adhesives.
Both trials were successful, suggesting that when mechanical recycling options are not available for healthcare plastics, value can still be realized through other recovery processes.
This article was originally published in Recycling Product News, April 2017, Volume 25, Number 3.