Tomra Sorting chosen by Monoworld Recycling Ltd as technology partner for groundbreaking new plastics recycling facility
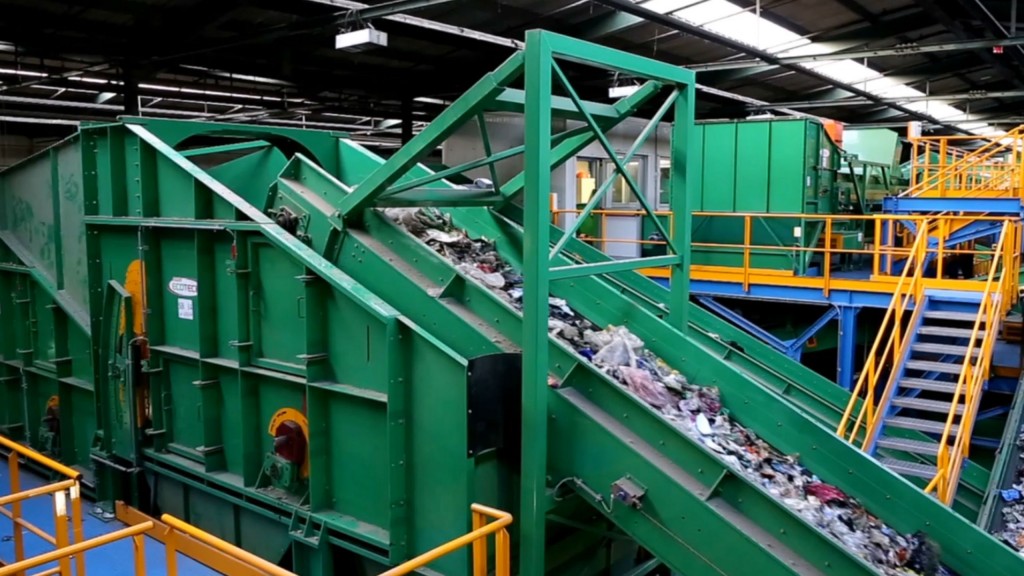
Global sensor-based sorting specialist, TOMRA Sorting, has been chosen by Monoworld Recycling Ltd (MRL) as the technology partner for a new £9 million state-of-the-art plastics recycling facility (PRF) in Rushden, Northamptonshire, England. Monoworld Rushden is the UK’s first mixed plastics to extrusion HDPE and PP recycling plant. The company also operates a film and metal sorting plant at Sharnbook in Bedfordshire.
The new 10tph PRF, which is based on a nine acre site with over 140,000 square feet of warehouse space, was built by the Italian AMUT Group. Officially opened in January 2016, the plant encompasses a post-consumer mixed plastics recycling facility, as well as a wash and granulation line. The plant has the capacity to recover up to 100,000 tonnes of recyclates annually. A total of 120 new jobs have been created at the site.
Sensor-based sorting technology is supplied by TOMRA Sorting with TOMRA’s AUTOSORT units installed to separate the mixed baled plastics into PET, HDPE, PP, film, paper, steel and aluminium. The PRF is capable of handling post-consumer pots, tubs, trays and mixed bottles, with TOMRA’s technology able to sort black plastics from the post-consumer trays. The black material is processed further downstream.
The recovered HDPE and PP materials are used in-house in the hot wash plant, producing high quality washed flakes which are supplied back to extrusion, injection moulding and pipe applications in UK and Europe. The other recovered material fractions – including PE natural and jazz and PET – are sold to customers throughout the UK and Europe.
Commenting on this major new investment, Claire Shrewsbury, Programme Area Manager for Plastics at WRAP, said: “This development represents exactly the type and style of recycling initiative that supports the UK’s drive to collect and recycle more non-bottle plastics arising from the domestic packaging waste stream. It is also firmly in keeping with the co-operative plastics recycling supply chain strategy outlined in the Plastics Industry Recycling Action Plan (PIRAP). The focus on effective separation of household plastics and further reprocessing of the polypropylene and polythene fractions will give local authorities and waste management contractors the confidence required to continue to increase collections of non-bottle household plastic packaging in support of UK plastics recycling targets through to 2020 and beyond.”
Nick Ruparelia, Commercial Director of Monoworld Recycling Ltd, adds: “This is a major step forward, enabling us to recover a significantly higher tonnage of material that can be processed in-house, and opening up new market opportunities for the sale of recycled material in the UK and Europe thanks to the enhanced material quality grades being produced.
“Over the 16 years that we’ve been operating, we’ve established strong relationships with many retailers, local authorities and waste collectors. With the drive to lower waste and meet increasingly challenging landfill and recycling targets, the volume of waste sent for recycling by local authorities and businesses has increased. And with local authorities increasingly favouring comingled dry recyclable collections (comprising paper, card, mixed plastics including pots tubs and trays and cans), there is greater demand for sorting facilities such as those found at our new Rushden PRF. Previously, we’ve only been able to process source-segregated materials at our recycling plant in Sharnbrook, Bedfordshire but now, thanks to the upgrade at the plant and the new TOMRA equipment, we’re in a position to accept and process all of the material from our retail, local authority and waste collection customers.”
Steve Almond, sales engineer at TOMRA Sorting, concluded: “Nick and his team took the right approach with this plant, working closely with TOMRA and AMUT from the very early design stages. They sent different grades of waste material to TOMRA’s test centre in Germany in order to design a plant that is capable of achieving the required quality and throughput, as well as producing the right quality of waste for use in their own plastics washing plant. We’re delighted to be part of this fantastic new facility, which is breaking new ground for plastics recycling in the UK.”